index / prev / next
< Tender Design >
I decided to start the tender construction before the engine body, because
it is likely that the castings for the tender will be difficult to obtain
suddenly. Actually it already became difficult to get small amount of cast
irons, so I adopt gunmetal as a material for the tender castings, except
wheels.
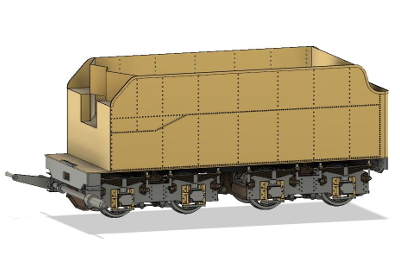
I obtained detailed drawings of the full size tender and designed my tender
according to the drawings.
There are about 350 parts for the tender chassis. Around fifty of them
are castings and other around fifty of them are laser cut parts. The rest
of them will be made from blanks. Their basic structure is the same as
prototype but my model has needle bearings in the axle boxes and thrust
bearings for the bogie pivots, because the tender receives additional weight
of a human driver. Regarding the brake system, full size tender has air
brake but my tender has foot brake which the driver operates. The brake
levers have the same arrangement as the prototype but operated by a foot
pedal instead of air cylinders.
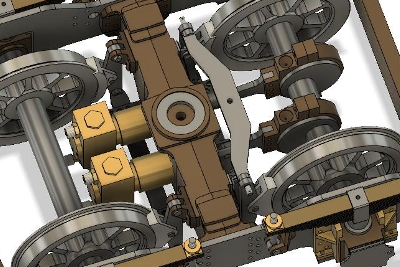
The axle driven pumps for which there are no space in the engine are included
in the tender. There are two pumps connected to an axle.
I worried about wheel lock due to load of the pumps. So I calculated the
possibility of it as follows.
The two eccentrics for the pumps are arranged in opposite phase (180 deg),
therefore the integrated load is the same as one pump, if mechanical resistance
is ignored. The pump bore is 13mm OD and its stroke is 16mm. So the area
of the bore is 133mm2 and the eccentricity is 8mm in radius. If the boiler
working pressure is 0.5MPa(=0.5N/mm2), the piston force is 0.5*1.33=66.5(N)
and the torque is 66.5* 8/1000=0.53(Nm).
On the other hand, the tender weight is around 55kg and driver's weight
is minimum 50kg, then the total weight is minimum 105kg. So the axle weight
is 105/4=26(kg). The wheel adhesive force is normally around 20% of the
axle weight, so it shall be 26*0.2*9.8=51(N). The wheel diameter is 102mm
and the radius is 51mm. So the torque is 51*51/1000=2.6(Nm).
The value is around 5 times larger than the necessary torque for the pumps
(0.53Nm), therefore the pumps are certainly driven.
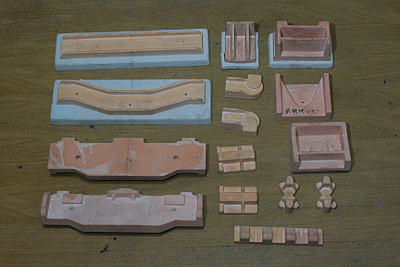
The tender is designed with 3D-CAD. As usual, the chemical wood patterns
for the castings are prepared by Modela CNC miller.
The material of the castings is gunmetal but only the horn blocks are made
of aluminum bronze, so as to avoid wear by friction against the gunmetal
axleboxes. In order to reduce the casting cost, both left and right horn
blocks are cast in a body (Bottom center parts of the photo).
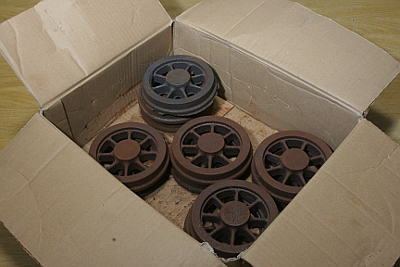
The wheels castings are the same as that of engine's bogie and pony truck.
They were already cast at the same time.
The photo shows laser cut parts for the tender chassis. Variation of the thickness is 1.2mm, 2.3mm, 3.2mm and 4.5mm. They come from Japanese standards.
index / prev / next