index / prev / next
< Boiler Repairs 3 >
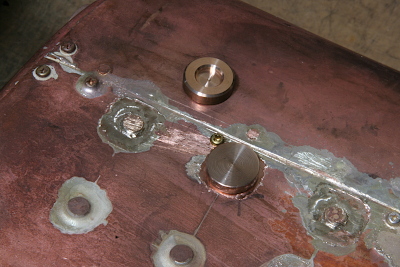
In order to stop leaks of the sidestays in the top row of the right outer
wrapper, I prepared caps to cover the sidestays' heads. The caps are phosphor
bronze tablets with recesses to clear the sidestays' heads.
Before soldering, the outer wrapper surface around the sidestays are trued up by endmill. Also some screw heads near the stays are cut flush and alternative screw holes apart from the stays are opened.

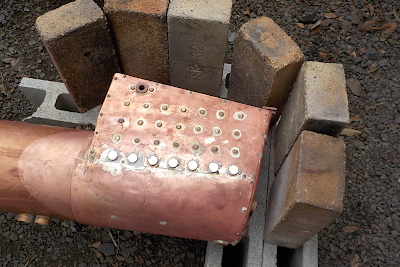
The caps are silver soldered. Also the alternative screw are caulked by
silver solder. Here I employed propane oxygen burner.
After that, other leak points are tried to repaired.
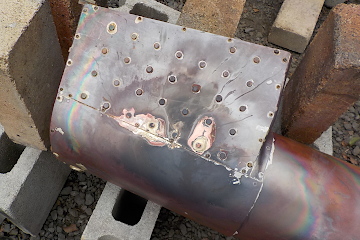
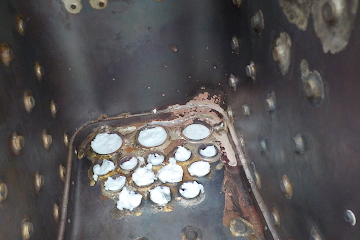
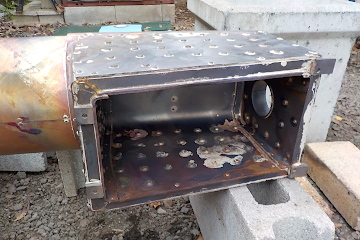
The 11th test was carried out. The additional caps exactly stopped leaks of the sidestays. But the other leak points remained after repeating three times repairs and tests.
I think the cause of new leaks is distortion of each joint due to topical expansion by topical heat. Such a large boiler made by relatively thin copper sheet causes large temperature distribution during soldering operations. Actually, when I soldered the backhead, small puddle had remained in the smokebox tubeplate. It means there was several hundreds degrees of the temperature distribution.
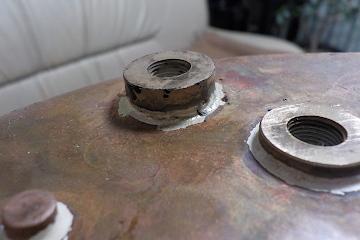
Especially, tubes, flues and long stays are affected by temperature distribution. After a lot of repairs, the smokebox tubeplate and the firebox tubeplate were distorted. The longstays became slack. The hollow stay push up the bush in the backhead. Maybe the sinkage of the sidestays is also caused by temperature difference between inner and outer wrappers.
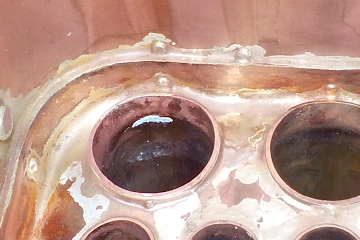
With each repair, distorted parts increased. The current most serious distortions are wrinkles at the back end of the flues. I guess it caused new leaks at the flues.
In order to stop distortions, I decided to stop silver soldering and utilize soft solder for future repairs.
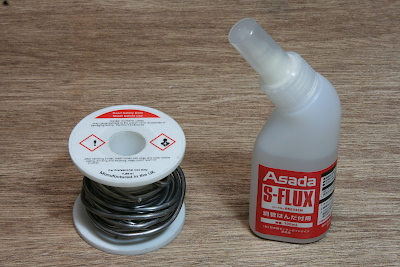
I obtained Johnson Matthey's Comsol from an ME supplier in UK. It is a kind of soft solder of Pb93.5/Sn5/Ag1.5 composition with 296 centigrade melting point. The flux is chosen for such high temperature soft solder.
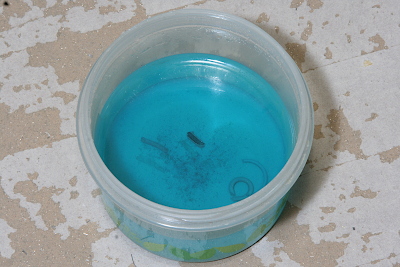
Typical soft solder is corroded in sulfuric acid. I pickled a piece of Comsol in dilute sulfuric acid for a couple of days and its surface was corroded. Maybe a short time pickling is no problem but I stop pickling just to be safe.
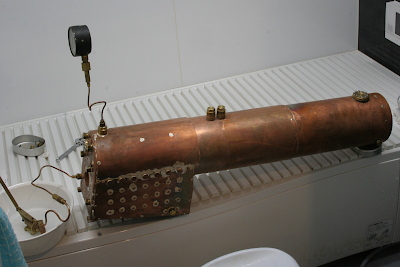
In order to confirm leak points, I did pressure test again. The pressure was raised to 0.1 MPa and I found several new leak points.
Surplus silver solder in the leak points were removed by small grinder, then it's ready for soft soldering.
index / prev / next