index / prev / next
< Smokebox Pipework >
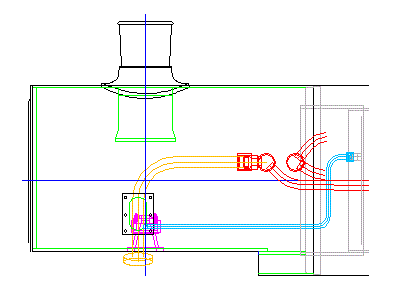
The smokebox pipework contains two steam pipes to the cylinder block, a
blast pipe, and a tube for the blower. First I made the steam pipes from
a 12 mm dia. copper tube. The pipes need seals between the smokebox inside
and outside. If some putty is applied directly between the pipes and the
smokebox wall, the pipes become unable to disassemble anymore. Therefore,
I prepared two blind patches that are in close contact with the smokebox
wall, and then the putty is applied between the pipes and the blind patches.
The holes on the smokebox wall must be large enough to let the cap nuts
of the steam pipes through.
The blind patches are made from a 1 mm brass sheet. Scribe the windows and holes, drill small holes, and bend with the bend roll so as to fit onto the smokebox curve.
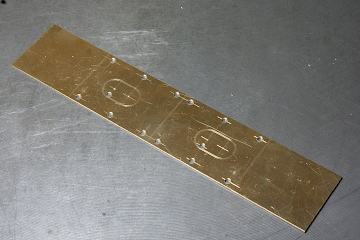
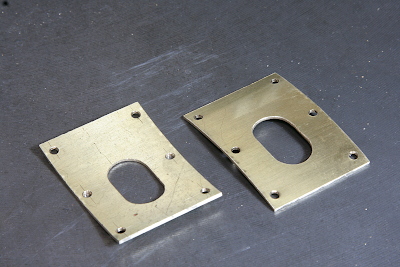
Cut out with a fret saw, then the blind patches are completed.
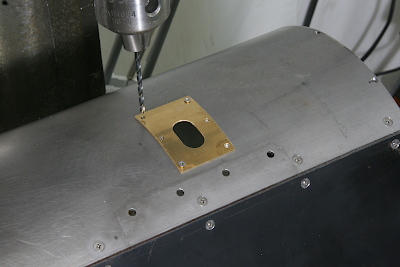
Set the blind patches on the smokebox and drill countersinks through the patches. Remove the patches, drill through smaller holes, and tap for screws. I employed M2.6 screws.
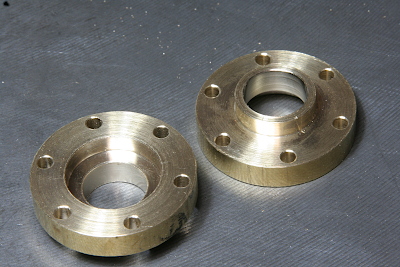
The steam pipes are connected to the cylinder block with rotatable flanges. The flanges are made from a brass round bar.
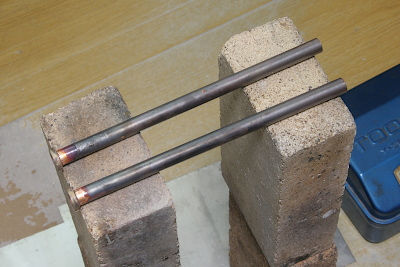
Before bending the steam pipes, "stub ends" for the rotatable flanges are silver soldered on the pipe bottom ends.

The steam pipes are annealed and bent with a handmade aluminum roller. Note that a drill shank is utilized in order to protect the pipe end.
The steam pipes have to be twisted with consecutive bends. It cannot be bent with a normal roller. The roller was modified and utilized as the photos show.
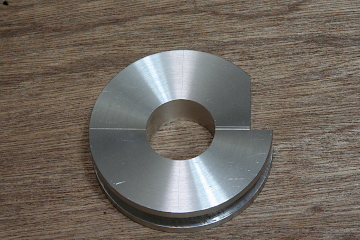
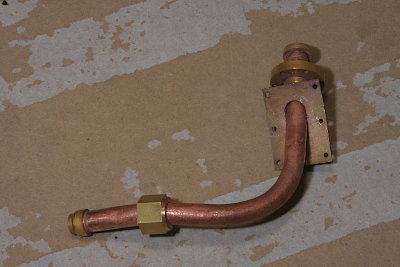
Insert the flange, the blind patch, and the cap nut on each steam pipe.
Finally, a brass ferrule is silver soldered on the other end of the pipe.
Insert the complete steam pipes from the holes at both sides of the smokebox. Connect both ends to the superheater and the cylinder block. Also fix the blind patches on the smokebox. In order to tighten the cap nuts in the narrow smokebox, I prepared a short wrench that was cut from a normal bargain wrench.
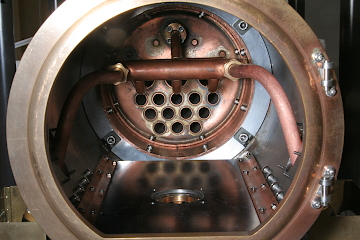
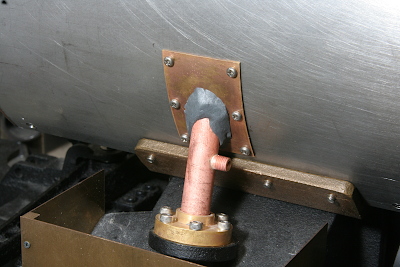
Close the gaps between the steam pipes and the blind patches with epoxy
putty. Note a silver soldered nipple on the copper pipe. That is for the
connection from lubricators. In the photo, the right-hand side is backward.
The blast pipe is made from a brass round bar. First, turn the outer profile in the lathe. The center hole is finished with a reamer in order to get a smooth surface.
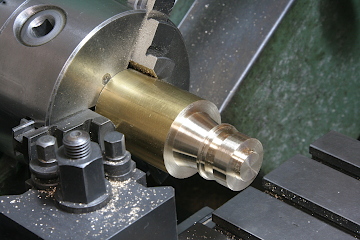
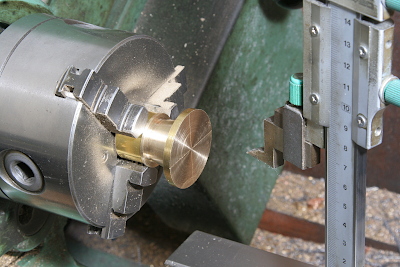
Part off, reverse, finish the bottom face, and scribe the center.
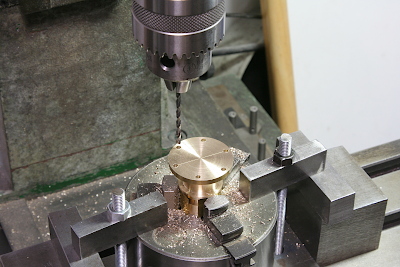
Fix the job on the milling table together with the three-jaw chuck. Align the center and drill circumferential holes with XY coordinate.
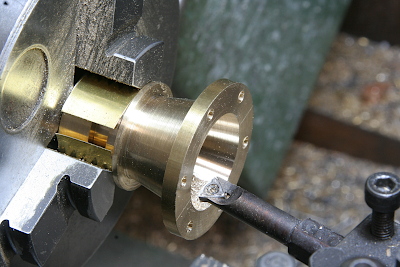
Return to the lathe and finish the bottom taper hole.
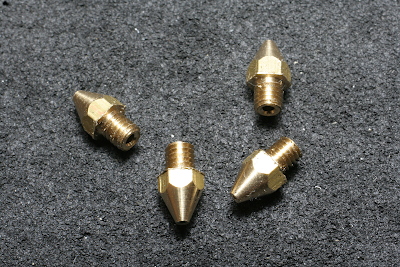
The blower nozzles are made from a 4 mm brass hexagonal bar. The tip hole is 0.5 mm dia.
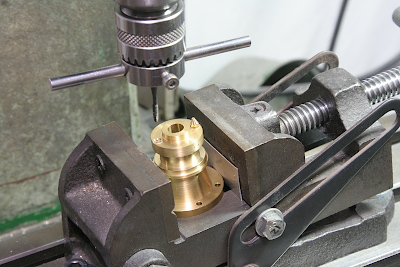
Drill and tap holes for the nozzles around the blast hole of the blast pipe. In order to tilt the holes, I employed the angle vise.
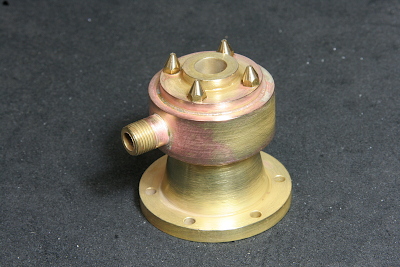
Silver solder a brass cylinder around the blast pipe so as to form a ringed room for the blower nozzles. Finally, a nipple for the blower is silver soldered on the cylinder.
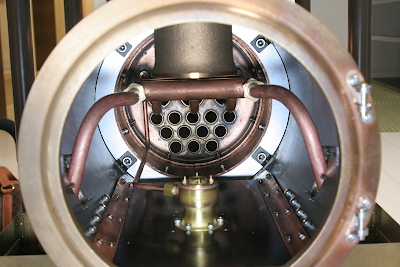
Bolt down the finished blast pipe in the smokebox. The blast steam comes directly through the hole of the cylinder block's top plate. The smokebox tubeplate and the blast pipe are connected by a copper tube with usual union connectors. Then the smokebox piping work is completed.
index / prev / next