index / prev / next
< Sandboxes 3 >
The sandboxes in this project function as oil tanks, so the lid needed
to be operable. I decided to replicate the real-life structure by incorporating
a latch mechanism. To give a clearer understanding of the process, here's
the completed result before detailing the steps.
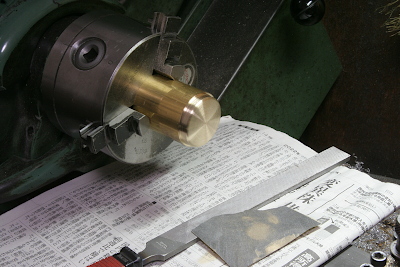
The lid has a diameter of 37mm and was crafted from a 40mm brass rod. The surface is curved, which I achieved by machining fine steps in the lathe and then smoothing the edges with a file to form the final curve.
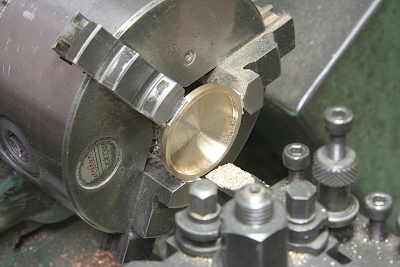
Part off, reverse, and counterbore the backside.
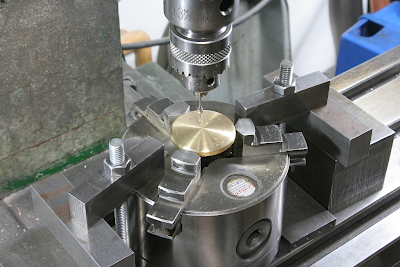
Next, I opened screw holes for attaching parts. By fixing the three-jaw
chuck directly on the milling machine table and aligning the center, I
drilled and tapped the screw holes using coordinate management.
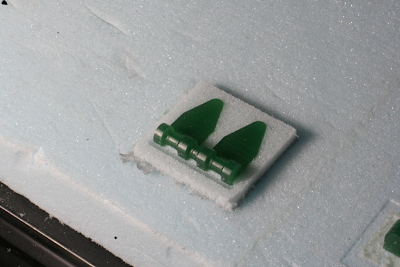
For the hinge and latch parts, which have more intricate shapes, I used lost-wax casting. Like with the sand traps, I machined the wax patterns using Modela. The photo shows the hinge part of the lid after front-side finishing and preparation for back-side machining.
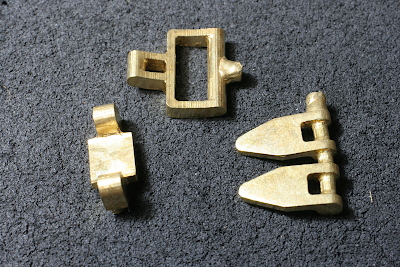
Here are the completed lost-wax castings. To save casting cost, each parts were made in pairs, making it tricky to identify them at this stage.
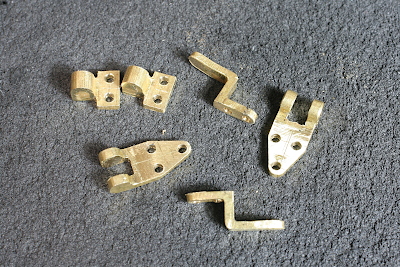
From the rough castings, I used a fret saw and files to refine the shapes and drilled the necessary holes. The two-hole parts are the hinges for the top plates, while the three-hole pieces are the lid hinges. The crank-shaped pieces are the latches for the handles.
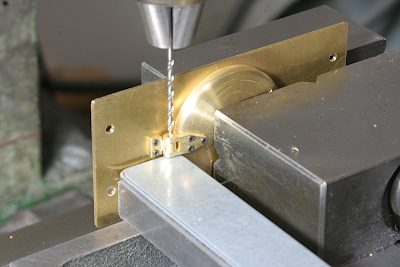
I attached the hinge parts to the lid and the top plate, aligning them to drill holes for the hinge pin. Due to the small size, careful drilling was needed to avoid deformation.
The hinge pins were made from free-cutting stainless steel rods. One end was threaded, and the other end was slotted for a screwdriver.
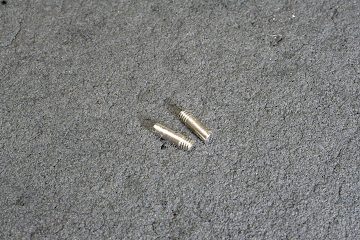
The pockets that limit the handle's angle were not cast but formed from a brass strip. Using steel flat bar to create male and female dies, I bent the brass strip in a vise to create the pocket shape. The end holes were drilled while the strip was still on the die.
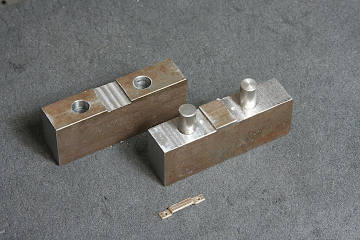
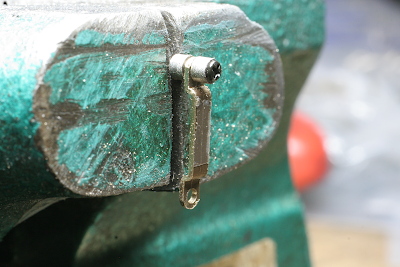
The edges of the pocket were rounded using "roller method". A
steel rod rollers are set freely at both sides of the hole with a screw.
While filing, the rollers rotate, preventing themselves from being filed,
thus only the brass is shaped to match the roller's profile.
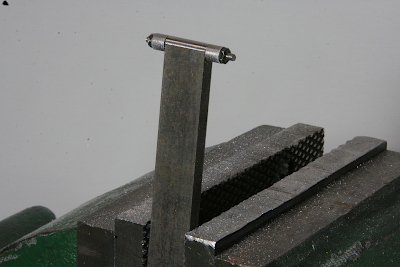
To shape the handle, I crafted a forming die. The ends of a flat steel were finished with a precise curve, again using the roller method.
The handle was cut from 0.8mm steel sheet and bent in stages. First, I bent it into a U-shape using the forming die, then added curves with a rod to achieve the final "ρ"-shape.
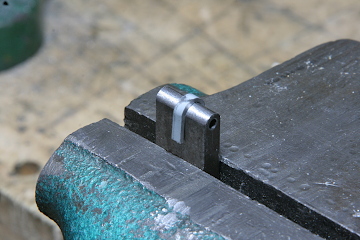
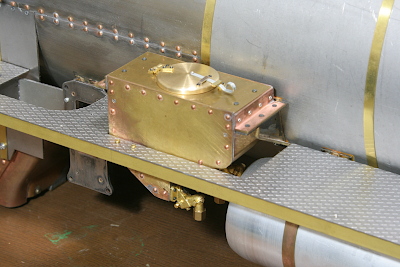
After assembling all the parts, the sandboxes were complete. I mounted them on the boiler covers and installed the running boards.
Next, I fabricated the ladder that attaches to the right rear side of the boiler. The left photo shows laser-cut parts, and the right photo shows the parts after machining. I also prepared patterned plate for the top step and rungs for the ladder.
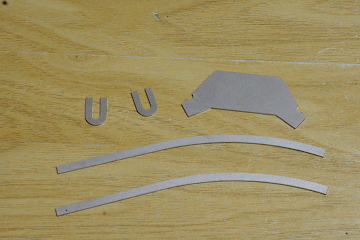
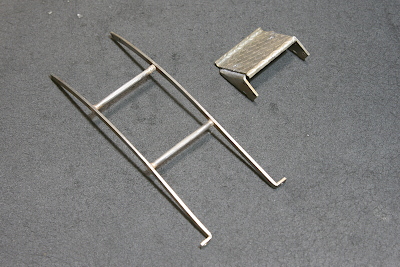
I silver-soldered the ladder body and the top step separately.
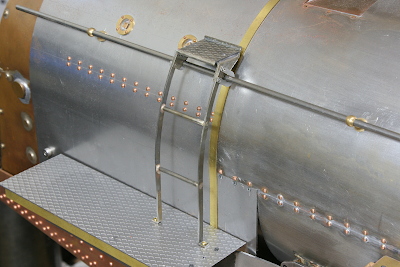
Finally, I attached the ladder assembly to the boiler. The bottom was fixed on the running board, while the top was secured to the handrail using U-shaped brackets.
index / prev / next