index / prev / next
< Pilot Deck 1 >
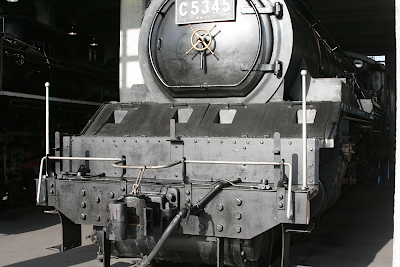
The pilot deck of the C53 has a unique shape that houses the Gresley valve
gear. The early models had a single-panel lower front, but they were later
modified to a four-section lift-up style to match the later models. I decided
to reproduce the appearance after the modification. Incidentally, C53 45
at Umekoji (pictured) has been restored to its original, pre-modification
form.
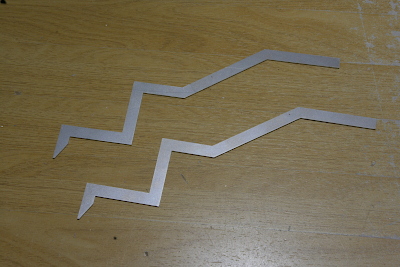
The stepped valances on the actual locomotive appear to be assembled by welding. To standardize the stepped shape, I made them as an integrated laser-cut part.
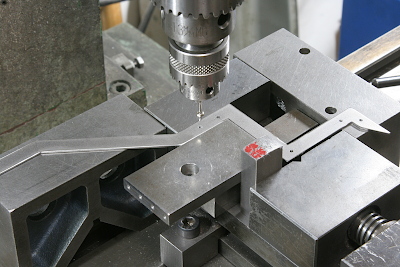
Holes for mounting screws were drilled into the skirt plates. Screws will be inserted from the back and the surface will be filed flush to remove any traces.
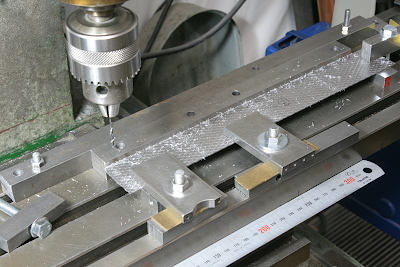
Mesh plates were used for both the lower and upper deck boards. These were cut out with a fretsaw, and necessary holes were drilled.
Obtuse-angle brass angles were required for the framing of the sloped sections. To bend brass sheets at an obtuse angle, I made a former from hard maple. Using the digital level, I set the angle vise to the required angle, clamped the wooden material, and machined it with an end mill.
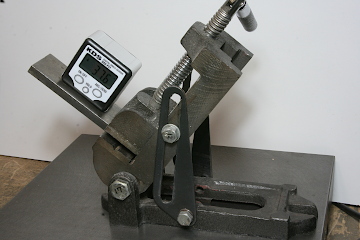
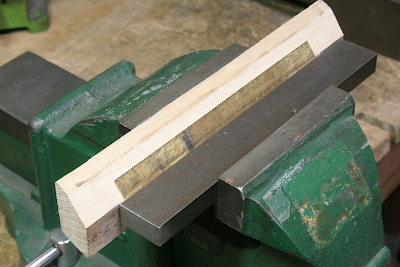
The brass sheets were annealed, and obtuse angles were created using the former. They were shaped by tapping with a plastic hammer.
A total of five obtuse-angle pieces were required. Holes were drilled in these pieces as well.
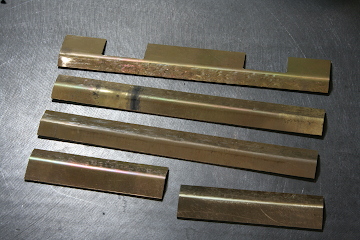
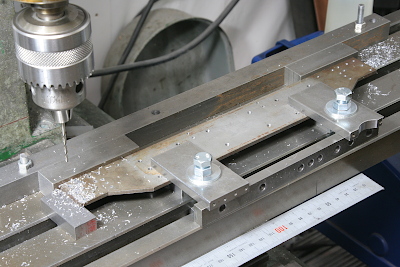
The front buffer beam was removed from the chassis, and holes were drilled to attach the pilot deck and other components.
Pillars for separating the lift-up panels were made by milling flat brass bars. There are five pillars supporting the four panels, and the central pillar is split into two sections.
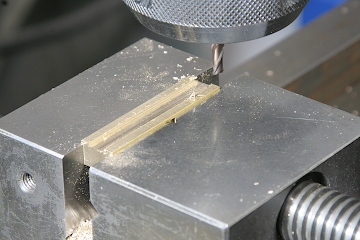
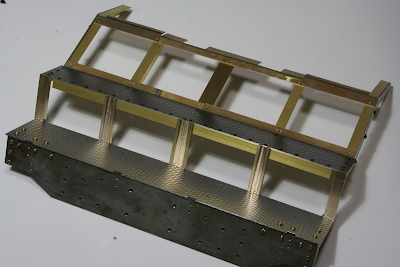
This is the assembled state of the parts up to this point. For the right-angle joints, additional brass angles were used.
Covers for the Gresley valve gear will be attached to the sloped sections.
Like the actual locomotive, hinges will be added so the covers can be opened.
Brass hinges intended for dollhouses were used for the hinges. The sleeve
part originally had four segments, but they were trimmed to three. In the
left photo, the left hinge is in its original form, the top-right hinge
is the trimmed version, and the bottom-right hinge has additional mounting
holes. The holes were drilled using the jig shown in the right photo.
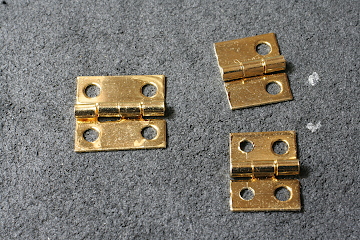
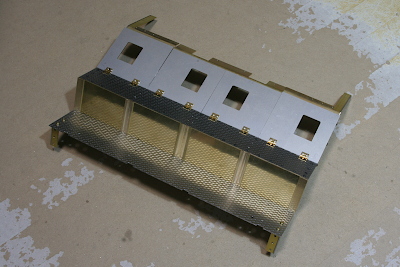
The valve gear covers are laser-cut parts with windows for integrating
steps. They were attached using hinges, as shown in the photo. Brass lift-up
panels were inserted between the front pillars.
The handles for the lift-up panels and the covers were created using lost-wax
casting. To reduce casting costs, four handles were made as a single piece.
The wax pattern is double-sided cut using the Modela and asked for casting.
Similar handles were produced in two sizes for use on the lubricator boxes
and other components.
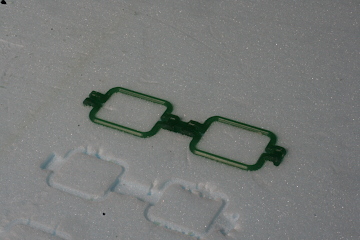
The handles were cut apart with a fretsaw, finished with files, and drilled for mounting holes. The right photo shows a handle mounted on a lift-up panel.
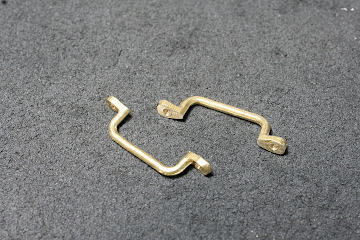
index / prev / next