index / prev / next
< Tender Chassis 2 >
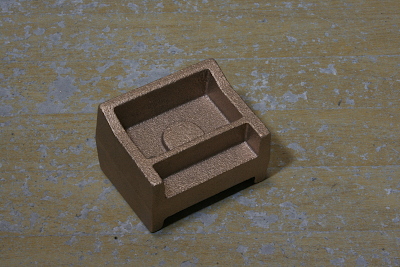
This is 'front casting' mounted at the front end of the frames and holds
front buffer beam and front coupler. It is also made of gunmetal.
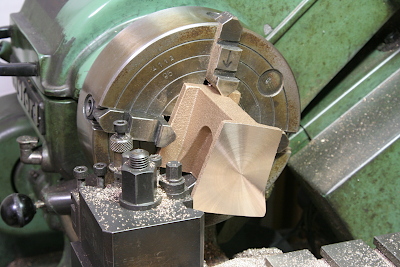
Cut the side faces in four-jaw. The both sides are finished parallel to each other utilizing four-jaw chuck's front face.
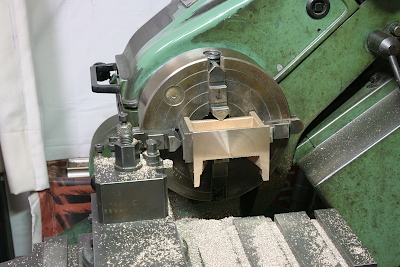
Chuck the side faces and cut the front face square to the side faces. The front buffer beam will be mounted on the face.
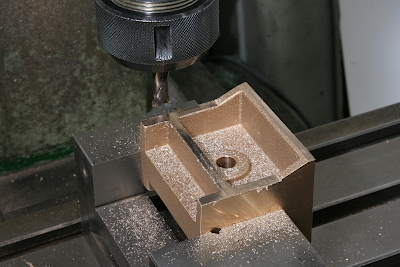
The top edges should be flush with the frame's top edge. So the top edges of the casting are cut to desired height. Here a hole for the front coupler pin is opened.
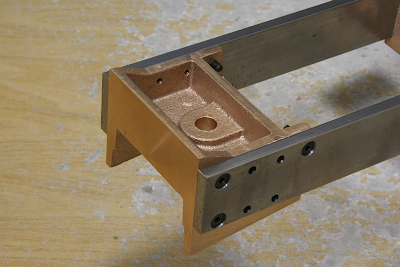
The finished front casting is mount between the frames. It is done in the same manner as the stretchers. There are seven screw holes in each side. Four of them are for fixing not only the frames but also steel angles on the outer faces of the frames. Note the rest three holes for only the frames are using countersink bolts so as not to disturb the steel angles.
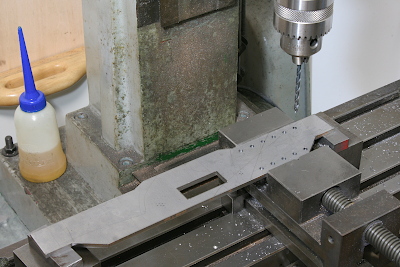
The front buffer beam is made from 4.5 mm steel plate. Holes for bolts are drilled due to x-y coordinates of the stage.
The steel angle size is 50 x 50 mm. The angle is truly square so they need
no correction. Cut off a piece by band-saw and finish by end mill.
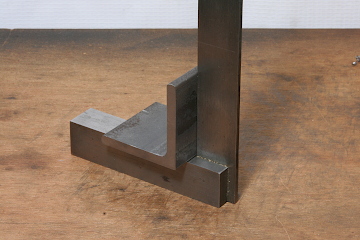
Cut a side of the angle to fit to the frame height. It is also cut by band-saw
and finished by end mill.
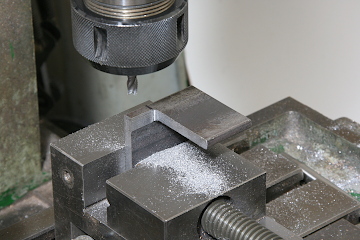
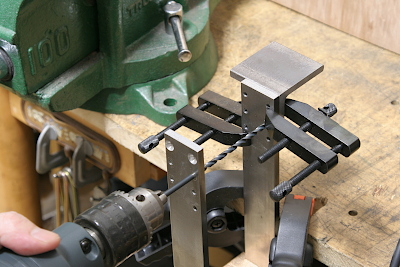
Drill the angle through the frames. The frames are already assembled, so
I employed a long drill so as to drill through the both frames.
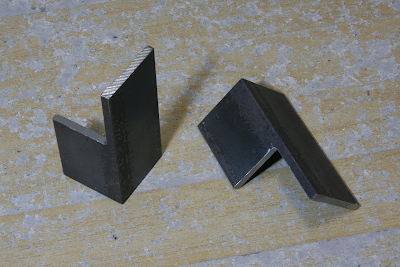
These are other steel angles which hold foot steps at both ends of the buffer beam. They are made from 40 x 40 mm angle. They also need no correction.
The front buffer beam and the angles are finally assembled. Inner and outer angles are arranged as the photo shows. Almost whole back face of the buffer beam is covered by the angles. Such a tough protection is necessary because the front buffer beam will hold heavy legs of the driver.
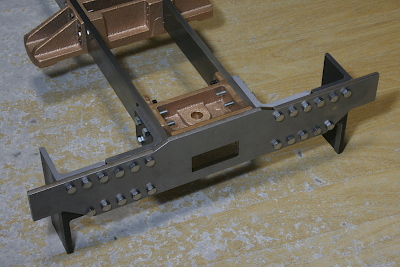
This is front view. In case of full size prototype, the angles at both ends are columns to hold elevating steps.
index / prev / next