index / prev / next
< Flanged Plates, Tubes and Flues>
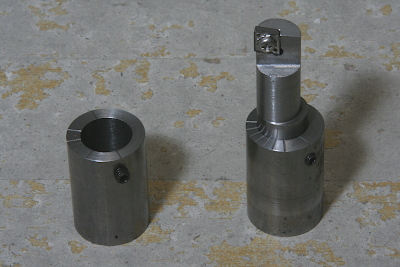
I prepared a home made boring bar in order to bore holes for tubes. The
bar can adjust its cutting radius with an eccentric sleeve. The tool shank
is secured in the sleeve by a set screw. I made two kinds of sleeves so
as to enforce coarse and fine adjustment.
The eccentric sleeve is chucked eccentrically in four-jaw and bored. After that the notches are cut by a disc tool chucked in a milling head mounted on the lathe table.
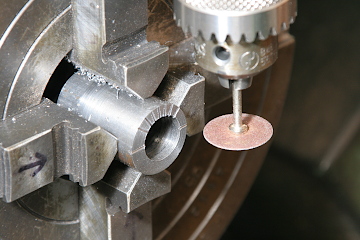
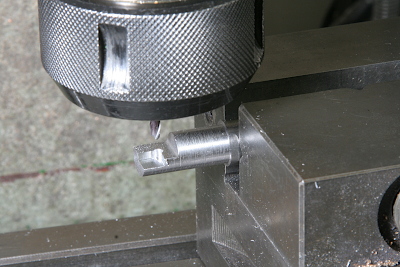
Tip of the shank is cut to be able to hold a carbide tip. The shank is
made of high carbon steel and is hardened and tempered.
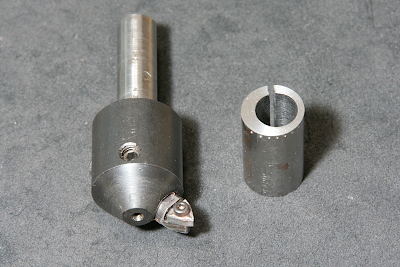
In order to bore holes for the superheater flues, I also prepared an eccentric
sleeve for a fly cutter. The sleeve is collet-type because set screw cannot
hold the large fly cutter firmly. The collet is squeezed in three-jaw.

Holes for the tubes are drilled 13 mm dia. and extended to 16 mm dia. with the boring bar. Hole for the regulator bush is also finished in the same way.
Holes for the flues are started with 25mm dia. holesaw and extended to
28.6 mm dia. with the eccentric fly cutter.
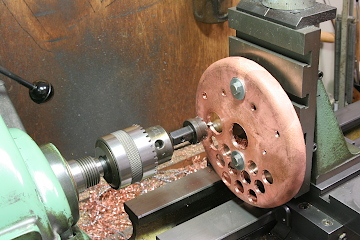
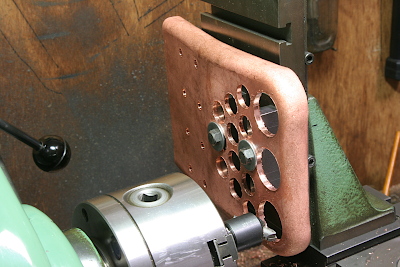
Holes in the firebox tubeplate are also opened. As slight steps are cut at the back ends of the tubes and flues, diameter of the holes are slightly smaller than the holes in the smokebox tubeplate.
Side faces of the flanged plates are trued up with end mill. Reproduce setup of making each former and screw down the flanged plate onto the former. And then it can be cut parallel to the former. The firebox backplate and the backhead is set on the tilt base plate.

The holes for longitudinal stay is tilt. So it is opened here. Before drilling,
cut a horizontal recess with an end mill.
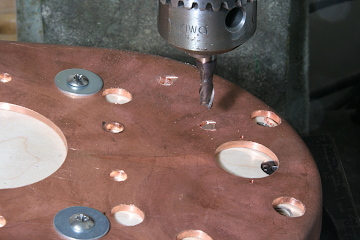
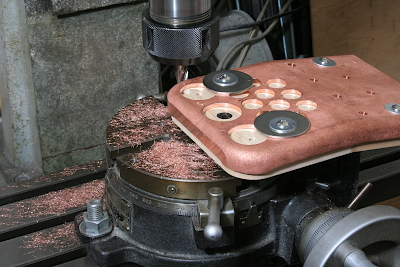
The firebox tubeplate is not tilt. Therefore the former is directly mounted
on the rotary table.
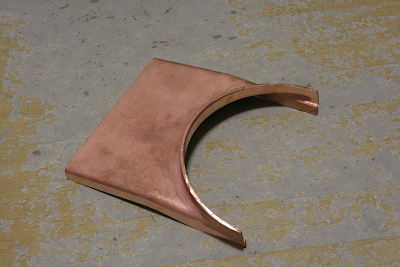
Truing up of the throat plate is a little complicated. So I show the result first. The inner face of the throat flange and the side faces of the parallel flanges were cut.
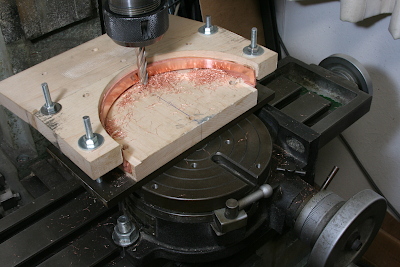
Sandwich the throat plate with front and back formers, and mount them on the rotary table and cut the throat inner face.
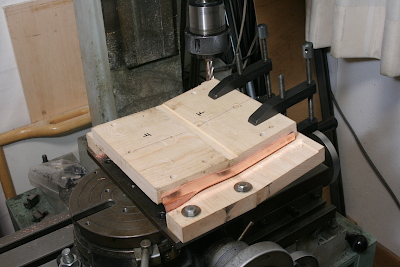
Reverse whole job and cut both side flanges, without rotating the rotary table.
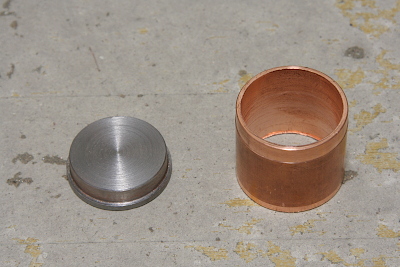
Here I make the tubes and flues. They need step cutting at their back ends. Before cutting, I prepared step diameter gauge and protection plug. The gauge is made from the same material of the tubes and flues. The step is 0.1 mm in design but the final diameter is determined by fitting it to the holes of the firebox tubeplate. The photo shows items for the superheater flues.
The tubes and flues are too long for my lathe to turn normally at tail end. So I turned them at root end. Turn shallow groove with a parting tool just after the chuck, turn a step from chuck side to tail side with a left hand tool, and then part off in the middle of the step. The photos shows turning a superheater flue.
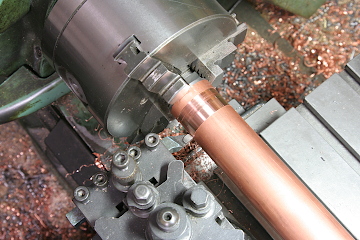
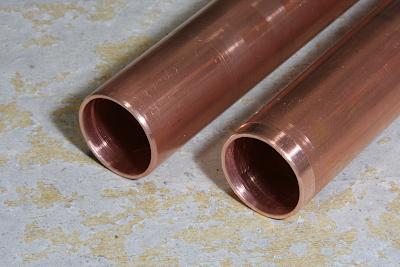
The photo shows both ends of the superheater flue. The left one is the
front end that is largely chamfered in order to ease pushing into the smokebox
tubeplate. The right one is the back end with a step that is also slightly
chamfered after parting off.
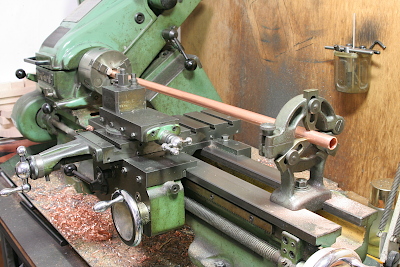
The tubes are also turned in the same way.
index / prev / next