index / prev / next
< Ashpan 1 >
The ashpan has a unique shape that intrudes into the rear pony truck. I
make it with stainless steel plates because the ashpan is the hottest part
of a loco except for the firebox. The body is made from 0.8 mm plates and
the bottom doors are made from 1.5 mm plates of SUS304 steel. The ashpan
is screwed down on the trailing frames, while the prototype ashpan is mounted
under the firebox. There are two rails at the top of the ashpan in order
to insert the grate from backward. The positioned grate is lifted up at
its back end and set into the firebox.
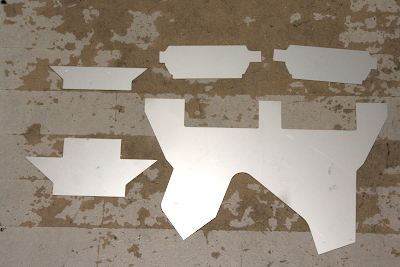
Some of the stainless steel plates for the ashpan body are prepared with
laser cutting.
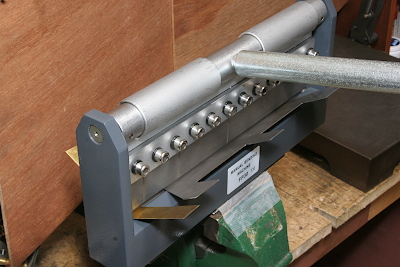
In order to bend the plates sharply, I got a sheet metal bender that can bend up to 300 mm width's plates. The maximum thickness for the stainless steel plate is 0.8 mm, which determined the thickness of the ashpan body.
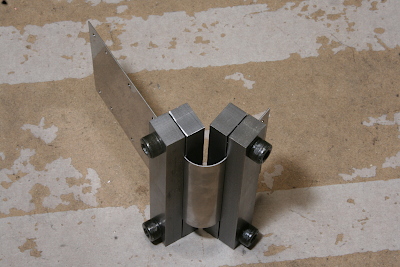
The bottom plate is bent with a 'radius'. Therefore I bent it with two pairs of steel flat bars.
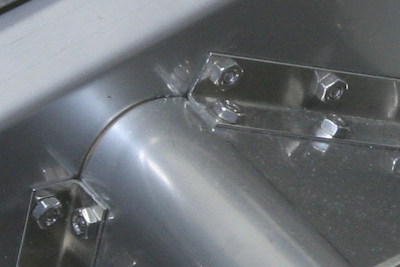
The body is assembled with stainless steel angles, screws, and nuts.
First, the side and bottom plates are drilled. After that, the angle is drilled through the holes of the plates.
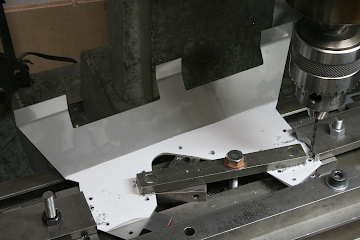
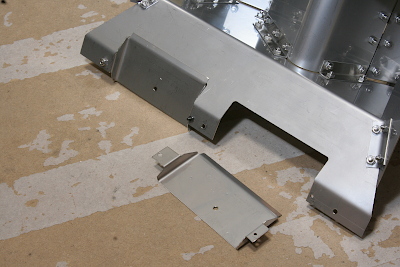
The four side pockets are prepared from other stainless steel plates and mounted on both sides of the ashpan top.
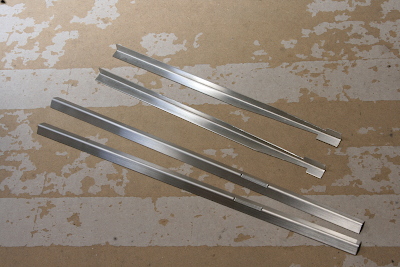
There are rails for the grate. They are made from 1 mm thickness stainless steel angles. The shorter two rails are for reinforcement.
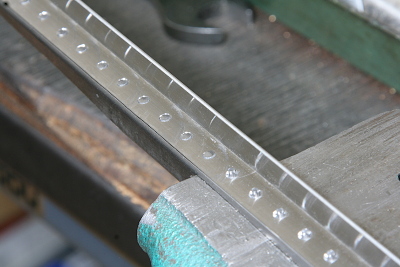
The guide rail and the reinforcement rail are gathered by a number of 1.6 mm steel rivets. The top face of the rail is countersunk and the rivet tips are sunk and filed flush.
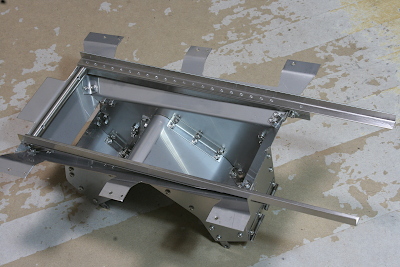
The rails are fixed on the ashpan. The top rails are extended backward in order to guide the grate.
The photos show how to fix the rails. The front ends of the rails are held by a stainless steel round bar, and the bar is fixed on the ashpan. The back ends of the rails are directly fixed on the ashpan with angles.
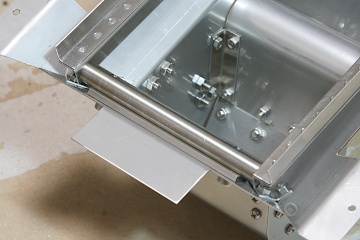
Brackets for the bottom door links are made from steel band plates. In order to finish the rounded ends, I adopted the 'roller' method. Sandwich a bracket with two rollers that rotate freely. File the bracket until the rollers start rotating, and the bracket is finished to the same radius as the rollers.
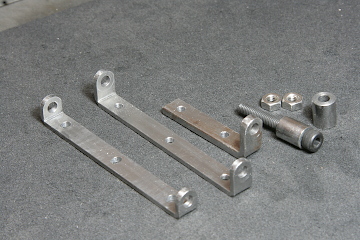
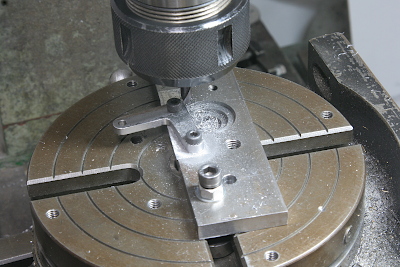
Only the L shape lever's radiuses are finished with the rotary table because they are difficult to apply files.
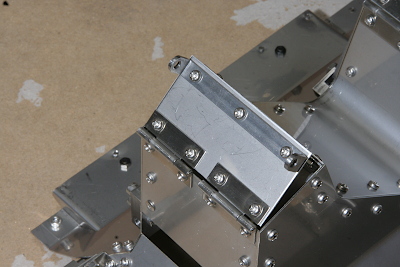
The hinges for the bottom doors are commercial stainless steel hinges.
The photos show opened and closed condition of the doors. The right direction is the front direction of the loco. When the push bar is pushed, the L-arm rotates, and the front door is pressed downward and opens. As the front and the back doors are synchronized with links, the back door also opens.
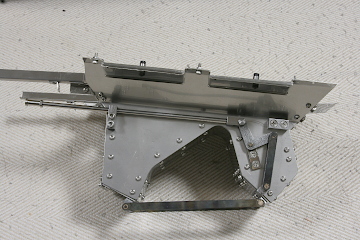
A coil spring is inserted between the push bar head and the bar guide. It pulls the bar and closes the doors normally. The spring is coiled in the lathe from 0.7 mm dia. hard stainless steel wire.
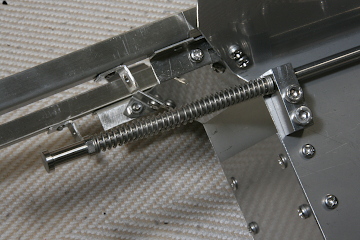
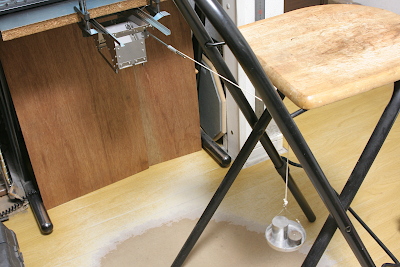
In order to design the coil spring, I measured the necessary force to close
the doors against the expected ash's weight.
The photos show top and bottom views of the finished ashpan. The installation on the chassis and the grate will be reported next time.
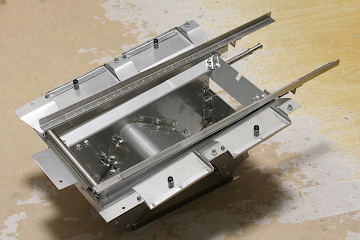
index / prev / next