index / prev / next
< Running Boards and Others >
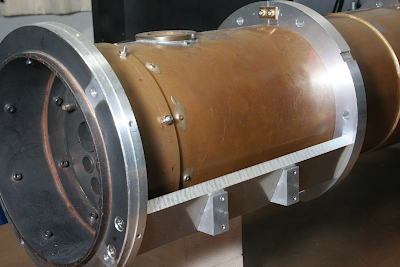
A power reverser will be installed at the front left of the boiler. Since
it receives force from the reversing link, I decided to mount it directly
on the boiler body, rather than on the boiler cleading, for stability.
However, instead of drilling holes into the boiler body, I placed a vertical
beam between the aluminum rings and attached the brackets there. The front
and rear brackets have a triangular cross-section, with the mounting surface
for the reverser being vertical. The following outlines the machining process.
First, I removed the tip ring and the first intermediate ring to drill holes, and tap threaded holes in the aluminum flat bar used as the longitudinal beam. The aluminum used is all duralumin, which allows for direct tapping.
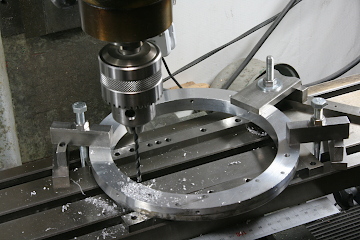
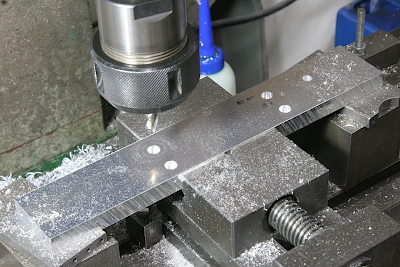
The brackets are secured to the longitudinal beam from behind using allen screws. To embed the screw heads into the longitudinal beam, I used an end mill to create counterbores on the back of the longitudinal beam.
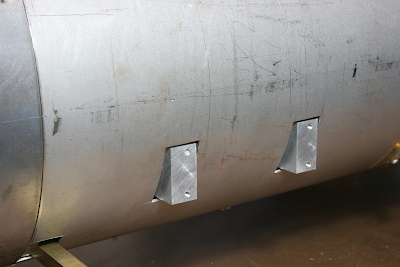
Once the boiler cleadings are installed, only the brackets are protruding through the windows.
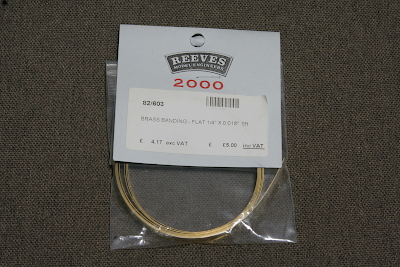
For the boiler band, I used 6.4mm x 0.5mm brass strip obtained from an ME supplier. Similar to the boiler cleadings, brass angles are attached at both ends and secured with screws.
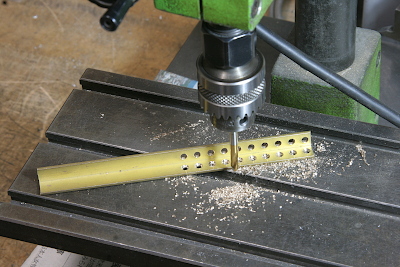
The brass angles are drilled before cutting. The photo shows the countersinking process for embedding copper rivets.
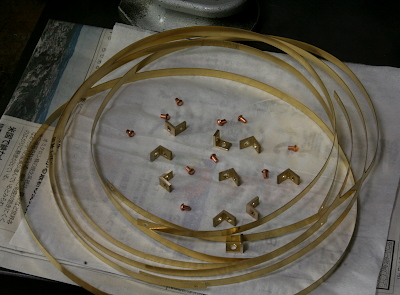
The brass strip is cut to the necessary length and drilled at both ends. I pickled the strip, angles, and copper rivets to prepare for soft soldering.
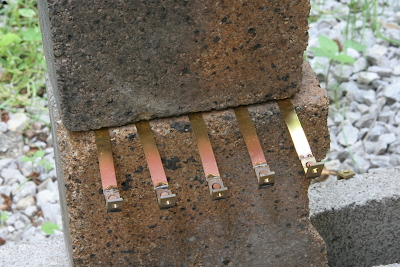
The brass strip and angles are fixed with copper rivets and reinforced with high-temperature soft solder.
The boiler bands are then attached around the boiler cleadings. The angles at the lower end are fastened with screws and nuts. The seams of the boiler cleadings are concealed by the boiler bands.
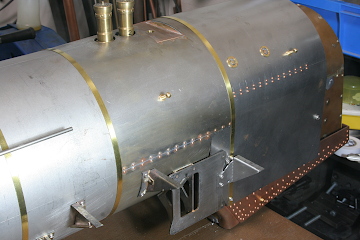
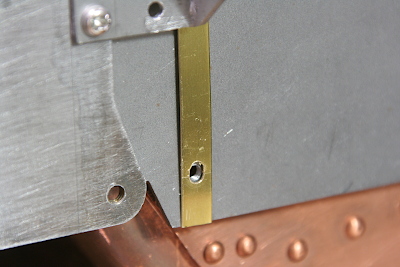
The boiler band around the firebox cannot be fastened at the bottom, so it is screwed to the boiler cleading at both ends. The holes in the boiler band are elongated to tighten and secure the band in place.
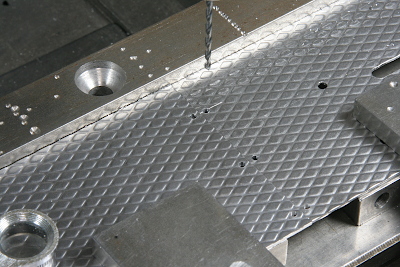
Next, I construct the remaining running boards using mesh plates from a supplier in Japan. The running boards have a step at the center, and the front half (lower section) has been partially completed. I cut and connect the remaining part of the front half. They are connected with a connecting strip on the back side. The front and rear running boards are aligned on the milling stage and drilled at a time.
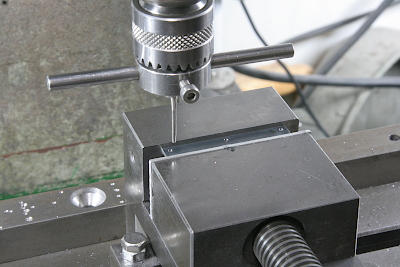
The connecting strip is cut from 1.6mm thick steel plate and tapped for M1.7 screws.

The valances of the running boards are made from brass angles and screwed from below to minimize visible fastening marks. The brass angles are drilled according to coordinates, and M1.7 screws are used here as well.
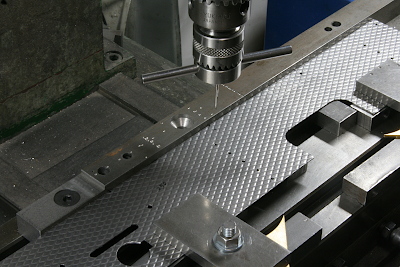
The fixing screws' positions for the valances on the running boards are drilled and tapped. All drillings for assembling the running boards were done using a milling stage for precise coordinate management, avoiding any transfer drilling.
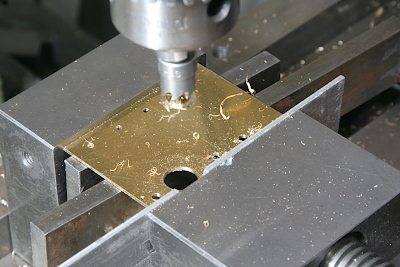
The vertical plates connecting the upper and lower sections of the running boards are made from brass plate. Holes are drilled for fixing, and additional round holes for piping are made using a hole saw.
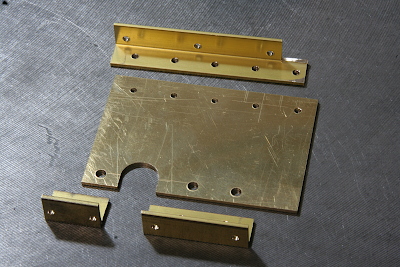
Shown are the finished vertical plates and assembly angles. The hole for the piping in the vertical plate is U-shaped.
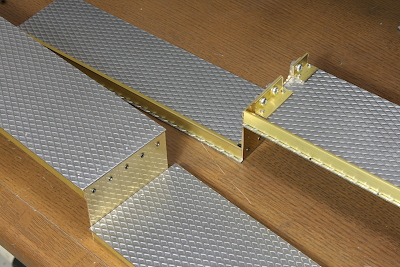
The step section is assembled, and the valances are attached. The left image shows the top view, while the right shows the bottom. The vertical plates protrude below the running boards, and the piping holes are below the running boards.
The assembled running boards are placed on the running board supports.
Final fixing requires the sandboxes and the cab, so it is temporarily assembled
for now. Once completed, it will be reinforced with soft solder.
index / prev / next