index / prev / next
< Steam Dome >
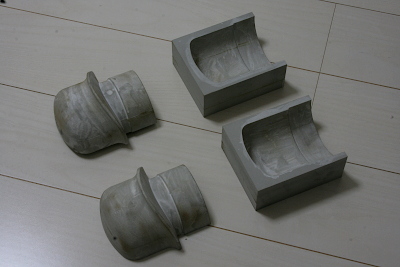
The steam dome has a diameter of over 130mm, so it is made of cast aluminum
alloy to reduce weight. As usual, I created wood patterns using the Modela.
I prepared the current patterns and cores to hollow out the interior. Both
are split into front and back sections.
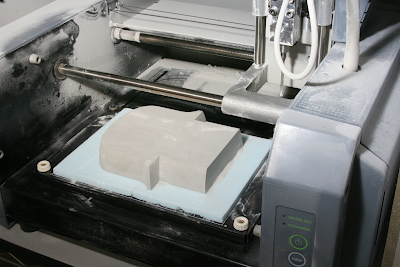
The photo shows cutting a chemical wood for the wooden pattern using the Modela. Since the pattern's height exceeds what the Modela can handle, I made it in sliced sections and later glued them together to form the pattern.
I requested a local foundry to cast the dome with aluminum alloy. The material used is AC4C.
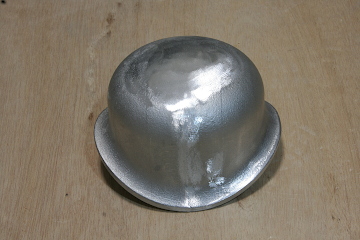
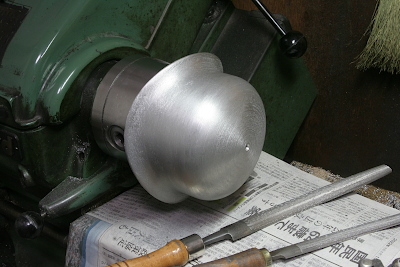
The entire casting surface of the dome is intended to be removed. First, I processed the top surface on a lathe. Using a four-jaw chuck, I gripped the inner circumference. The curved surface was machined in fine steps by calculating the coordinates, then finished with a file. The lower part is saddle-shaped, so after finishing the front and back edges, the sides were left unmachined. At this stage, I also drilled the central fixing hole.
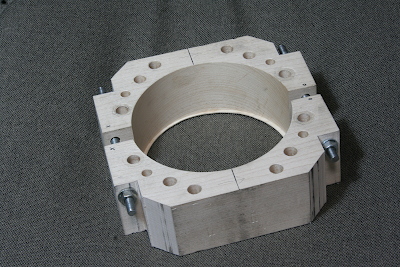
To machine the seating surface, I prepared a wooden fixture to hold the dome by its outer circumference. The material used was hard maple. First, I'll explain the process of making this fixture.
I cut out the outer shape with a bandsaw and drilled fixing holes, inserted a steel flat bar in between, and fixed it to the faceplate of the lathe, centering it. In this state, I traced the outer shape of the wooden pattern onto the faceplate with a fine marker pen. Then, I dismantled it, cut out the central hole roughly with a bandsaw, set it up on the faceplate again, and finished it with a boring tool.
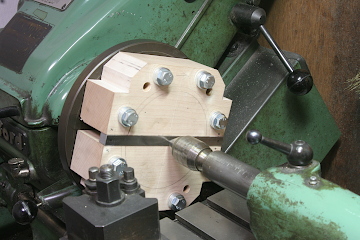
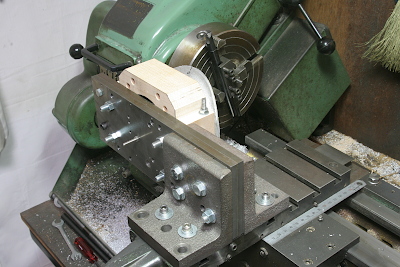
As shown in the photo, I attached angle plates and flat steel plates on the cross slide and set up the wooden fixture, securing the dome to finish the seating surface. Due to the large size of the workpiece, I have to set it up with a significant overhang to the left of the cross slide. Both the angles and flat plates are large to enhance rigidity.

I used a boring tool mounted in a four-jaw chuck as a fly cutter. The cutting radius was the same as the boiler cleading's radius, and since it exceeded the lathe center height, I utilized the gap in front of the bed for clearance. Therefore, I could only machine half the dome seating circle at a time, requiring me to rotate it 180 degrees to machine the other half.
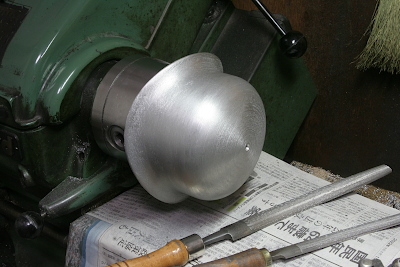
Finally, I finished the outer sides of the lower edges with files. Here, I held the inner circumference with a three-jaw chuck, but I only used the lathe as a workbench, not rotating it. I filed the edges down to under 1mm thickness and finished with emery cloth.
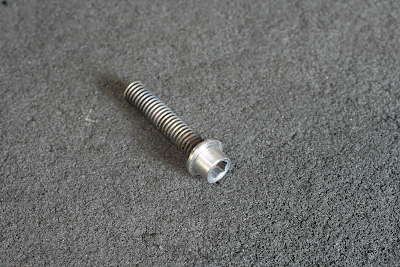
The dome will be bolted onto the inner dome. To resemble the actual cap nuts, I modified an M4 hex socket head bolt. I used a steel bolt and turned it in the lathe after annealing.
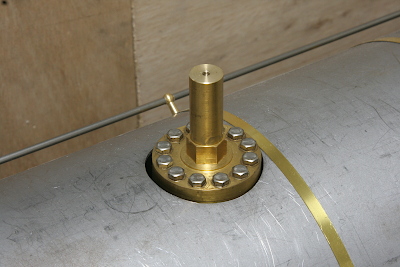
The spring pocket at the tip of the inner dome was finished to a length by matching it to the dome, and an M4 threaded hole was drilled and tapped at the tip.
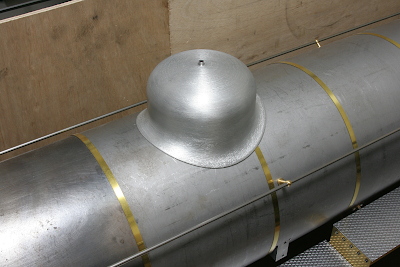
Here is the steam dome mounted. The lower edge fits tightly against the
boiler cleading without any gaps.
index / prev / next