index / prev / next
< Air Reservoirs >
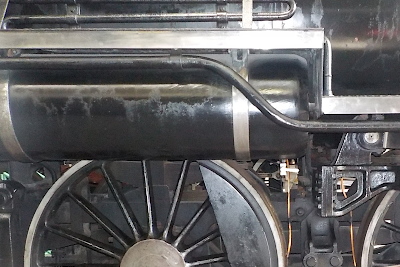
The photo shows an air reservoir of a full size C53 locomotive. I prepared
this large dummy components using aluminum alloy to reduce weight, and
was made from aluminum pipes and bars. The same size of aluminum pipes
will also be used for the heat exchanger.
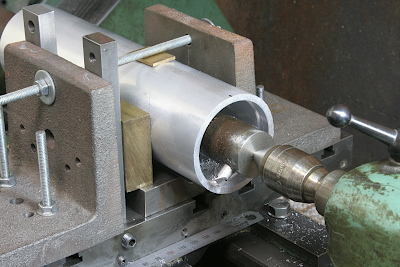
Aluminum is prone to scratches, so careful handling during processing is essential. It is necessary to cut steps on both ends of the pipe inside. When using the lathe spindle to chuck the pipe and support opposit end with a fixed steady, the outer surface tends to get scratched. To prevent this, I used "horizontal boring" approach. The pipe was fixed on the carriage, and a round bar was held between the spindle and tailstock, with a cutting tool mounted to the bar for machining. This is a method used for boring cylinder blocks.
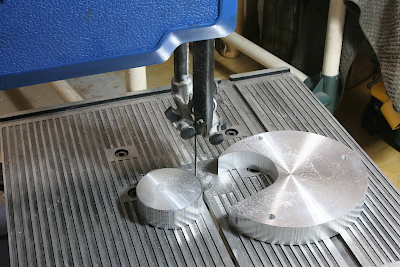
A disk was prepared to support the machined inner circumference. The material was surplus from the aluminum rings on the boiler, cut by a band saw.
The disk was finished with a tapered outer circumference and a tapered hole to fit the tailstock’s live center. To ensure the taper angle was accurate, I used a square and dial gauge as shown in the photo to align the top slider's angle with the live center's taper. The square was placed between the dial gauge and the live center to prevent measurement errors due to any misalignment in the dial gauge’s height. In this state, the disk was finished with a boring tool by moving with the top slider to refine the tapered hole. The photo on the right shows the completed disk.
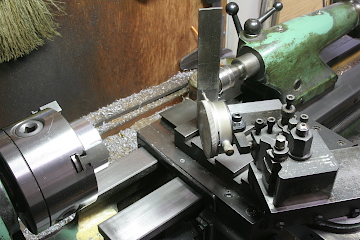
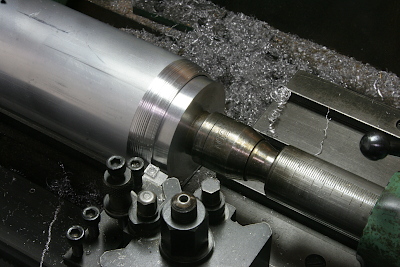
The disk was used to support the inner circumference of the pipe while
machining the outer profile. First, cut detailed steps as calculated.
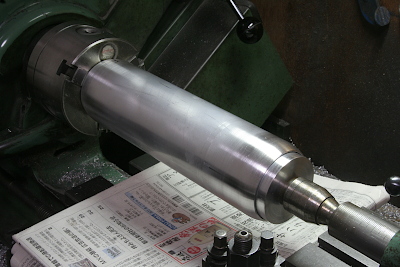
The steps were smoothed with a file and emery cloth, resulting in a smooth
curve. The same process was applied to the opposite end.
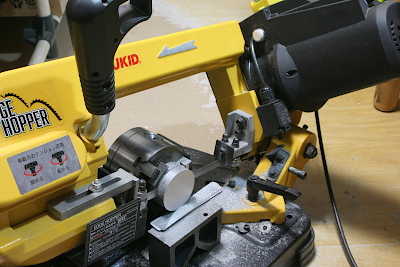
Next, head plates were prepared. Using round bar material that was prepared
beforehand, it was sliced into discs with a band saw. The band saw is a
different type which is primarily used for cutting long materials.
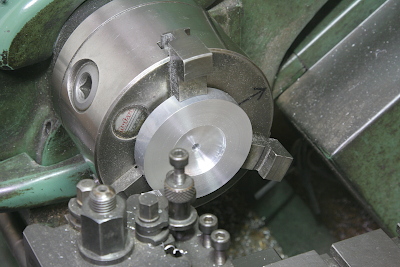
Processing began on the back side of the head plate. The surface was cleaned, a center hole was drilled through, and a step-machining was applied to allow for three-jaw chucking during front side processing.
The plate was reversed to chuck the previously machined step and finish the outer diameter. Finally, the front curved surface was processed. Similar to the pipe, detailed steps were cut first, and then the curve was finished with a file and emery cloth.
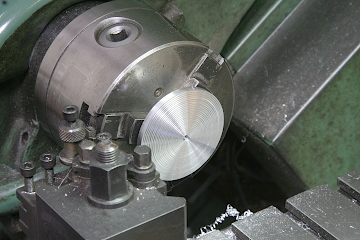
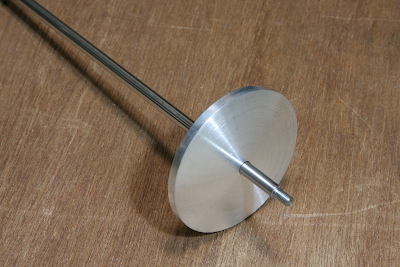
The head plates on both sides are held together with stainless steel shafts,
with screws threaded into both ends.
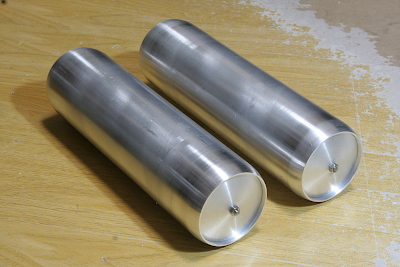
The air reservoirs are temporarily assembled with nuts on both ends, but
will eventually be secured with components resembling elbow joints.
The air reservoirs are held with brass bands, and brass straps were created
to secure the ends of the bands. Two straps were combined and processed
with a rotary table. The left photo shows before and after processing.
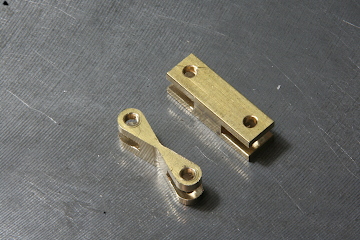
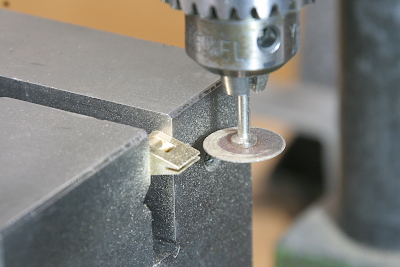
The work was cut into two pieces and a slit was created to insert the band.
A 0.5mm sanding disc was used for this task.
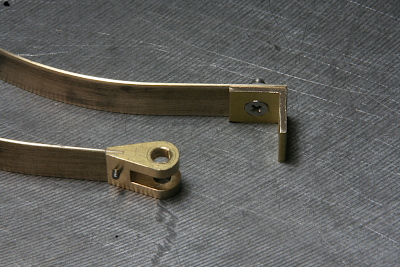
The straps are used for only the outer side of the bands, while the opposite
side is supported with brass angles. The brass band was screwed in place.
Since suitable width brass bands were unavailable, they were cut from 0.5mm
brass sheet.
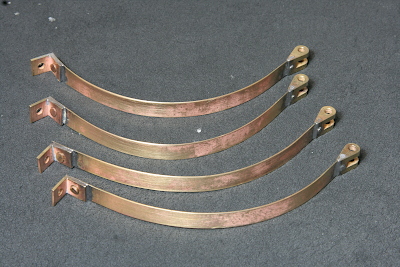
Finally, high-temperature soft solder was applied to reinforce both ends.
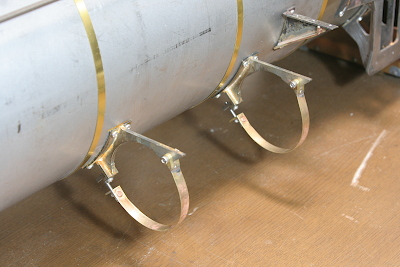
Only the bands were initially installed under the air reservoir brackets on a boiler cleading. The brass angle sides allow the bands to be tightened with screws.
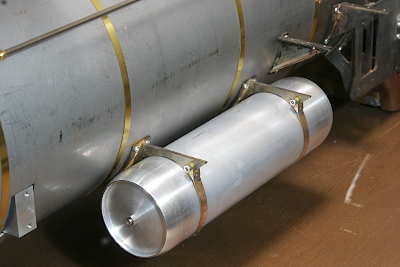
The air reservoirs were then inserted, and the bands were tightened. As
the reservoirs are secured only with the bands, nuts will be added to the
ends of the tightening screws to prevent loosening.
index / prev / next