目次 / 前月 / 次月
2020年8月 「フランジプレートと煙管」
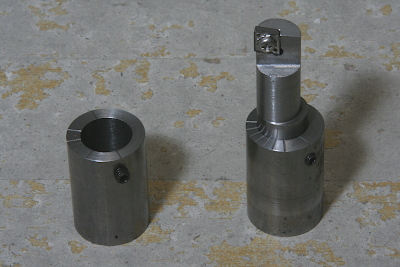
小煙管用の穴(16mm)を仕上げるため、ボーリングバーを自作した。偏心スリーブに対するシャンクの固定角度を変えることで、振りを微調整する構造である。シャンクはセットビスで固定される。偏心量の多い荒削り用のスリーブと、偏心量の少ない仕上げ用のスリーブの2種類を用意した。
偏心スリーブは、丸棒を四爪チャックで偏心させて旋削し、モーターツールのディスクビットで溝を入れる。ミニフライス盤を旋盤のテーブルにねじ止めすることで、複合機械として使用した。
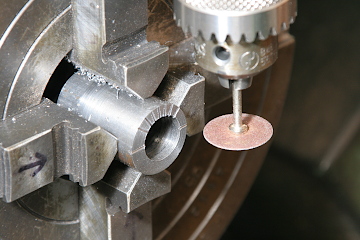
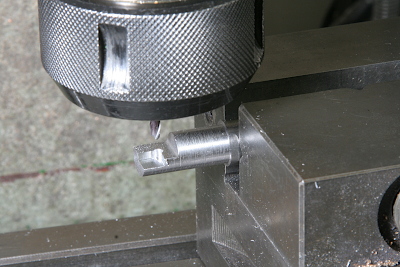
シャンクの先端は、スローアウェイチップをねじ止めできるようにエンドミルで加工する。シャンクの材質はS45Cで、加工後に焼き入れ、焼き戻しをした。
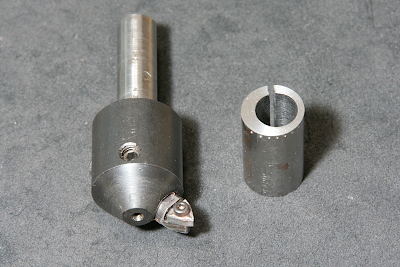
大煙管用の穴(28.6mm)を仕上げるために、フライカッターを偏心させるスリーブも用意した。こちらはセットビスで止めきれないので、スリ割りを入れて三爪チャックで締め付けるコレット構造にした。

小煙管用の穴は、ドリルで13mmの穴を開け、ボーリングバーで16mmまで拡大した。煙室管板の加減弁ブッシュ用の穴も、同じ手順で仕上げる。
大煙管用の穴は、ホールソーで25mmの下穴を開け、偏心フライカッターで28.6mmに拡大した。
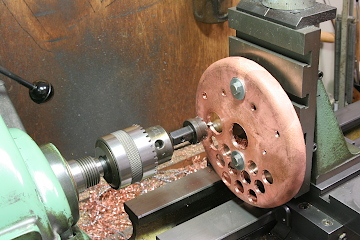
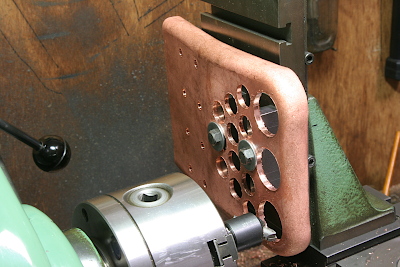
内火室管板も同様に加工するが、内火室側は煙管先端の段差加工をするので、仕上げ径は煙室管板より少し小さくしている。
フランジプレートのフランジ面をエンドミルで仕上げる。型板を加工した時と同じセットアップを再現し、型板にフランジプレートを取り付けることで、型板と平行に加工することができる。内火室後板とバックヘッドについては、ベースプレートを挟んで傾けた状態で加工する。

バックヘッドのロングステイ用の穴は、斜めに開ける必要があるので、ここでついでに開けておく。まずエンドミル先端で平面を掘り、センタードリルで位置を決めて、通常のドリルで穴を貫通させた。
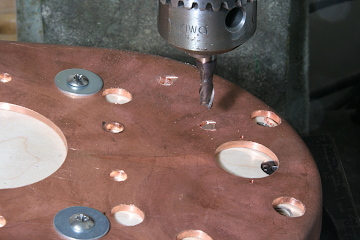
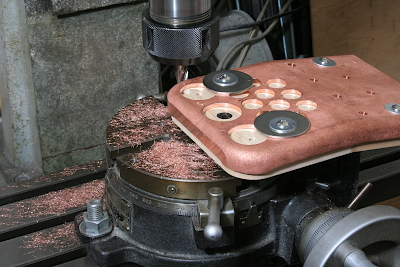
内火室管板は傾いていないので、型板を直接ロータリーテーブルに取り付けて加工する。
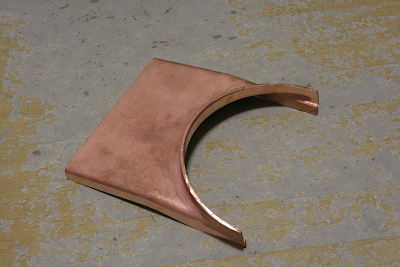
喉板の加工はややこしい。わかりやすいように、先に完成品を示す。加工が必要なのは喉の円弧の内周面と、左右のフランジ部分の側面である
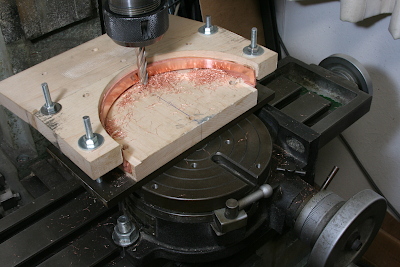
喉板を前後の型板で挟んで、ロータリーテーブルに取り付け、喉の内周面を加工する
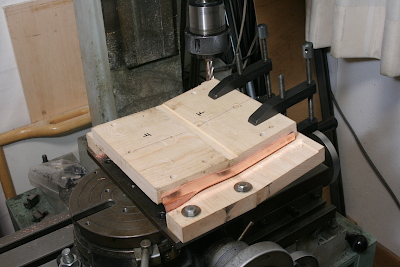
そのまま型板ごと反転して取り付け直し、左右のフランジ側面を仕上げる。ロータリーテーブルは回転させずに使用する。
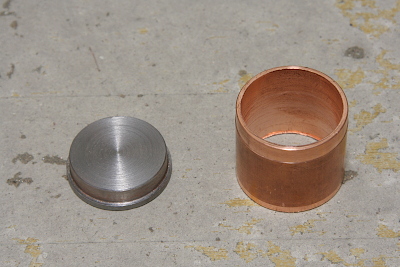
ここで煙管を準備するが、火室側の段差加工が必要である。加工に先立って、段差加工ゲージと、保護用プラグを用意した。ゲージは煙管と同じ材料から作ったもので、設計上の段差加工は半径で0.1mmだが、管板の穴とはめ合い確認をして直径を決めており、加工する煙管はこの直径に合わせる。プラグは煙管を三爪チャックした際の変形防止のため。写真は大煙管用で、小煙管についても同様である。
煙管は旋盤のベッド長ぎりぎりで、右端を加工することができないので、根元側を加工する。チャックぎりぎりに突っ切りバイトで溝を入れ、そこから左勝手バイトで右に向かって段差加工をした。これを突っ切って仕上げる。写真は大煙管を加工しているところ。
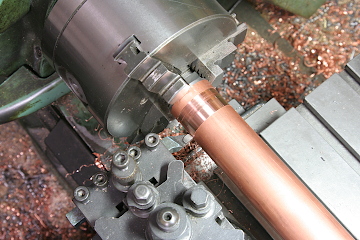
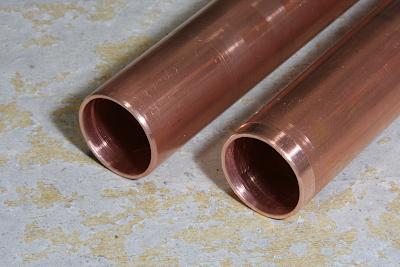
写真は加工後の大煙管の両端を比較したもの。左が前端で、煙室管板に入れやすくするため、外周を大きく面取りしている。右が後端で、段差加工して突っ切った後にこちらも軽く面取りをしている。
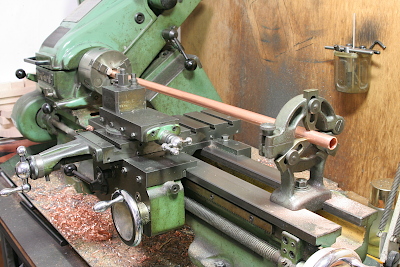
小煙管についても全く同じ手順で加工を実施した。
目次 / 前月 / 次月