目次 / 前月 / 次月
2018年4月 「バルブギア(4)」
第二動輪クランクピンに取り付けるリターンクランクは、特殊な形状をしている。クランクピンへの取り付け穴はスリ割りが入っていて、ボルトで締め付けて固定されるが、ビッグエンドの端面は、ボルトの穴と同心円のアール加工が施されている。スモールエンドのピンは、ロックタイト648で接着した。
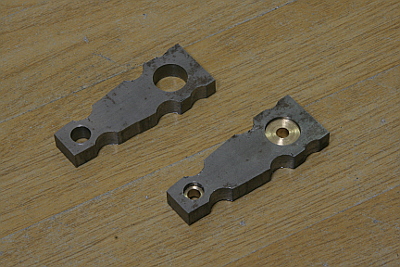
まず平鋼に穴を開け、事前に内アール加工をして、不要な部分を切り落とす。真鍮のブッシュは、加工時に治具に固定するための径調整用ブッシュである。
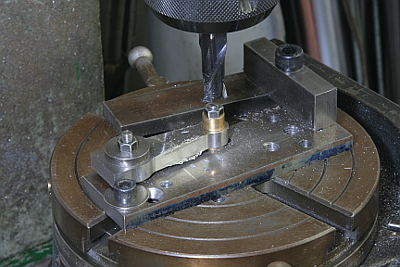
スモールヘッドはいつものようにロータリーテーブルで加工する。
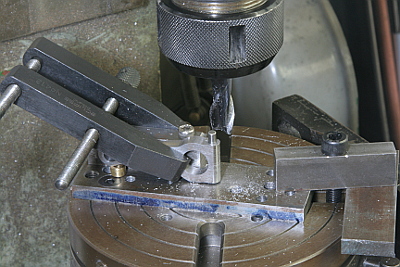
下の端面のアール加工。これもロータリーテーブルを使用する。平鋼を組み合わせて低いアングルを作り、、そこにリターンクランクを押し付けて固定した。
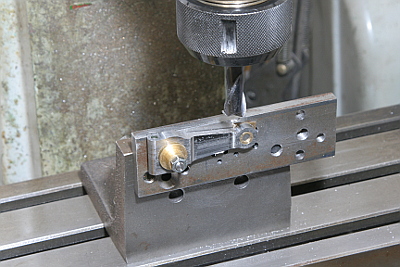
最後に側面中央部を薄く削れば、加工終了。
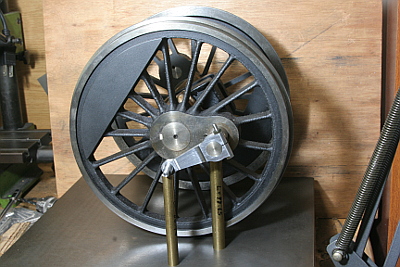
ここでリターンクランクの角度を仮決めする。第二動輪を外して定盤上に置き、長さを調整した真鍮丸棒2本で、リターンクランク角度を決める。まずクランクピン側の丸棒で、クランクピン高さを主軸高さに合わせ、その状態でリターンクランクの先端軸が所定の高さになるように、リターンクランク角度を決める。ちなみにバルブギアの設計は、基本的に実機のスケールダウンどおりにしている。
エキセン棒の軸距は現物合わせで決める。軸距測定治具は、2本の平鋼を長穴で接続して長さの微調整ができるようにしたものである。第二動輪のクランクピンの前後死点位置で、いずれも加減リンクが中立位置(弁心棒を上下に動かしても弁が動かない位置)になるように軸距を決める。前後の死点で軸距が異なる場合は、前の工程で決めたリターンクランクの角度が悪いということになる。
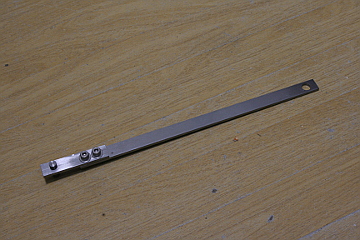
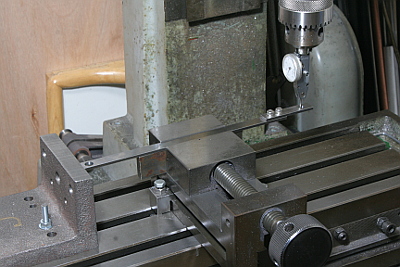
測り取った軸距をそのまま材料に移し開けるのではなく、いったん数値化した。フライス盤のステージに治具を保持して、テコ式ダイヤルゲージで穴位置を主軸と正確に一致させ、両端の穴の座標の差から軸距を計算した。公式側と非公式側で、約0.6mmの差があった。
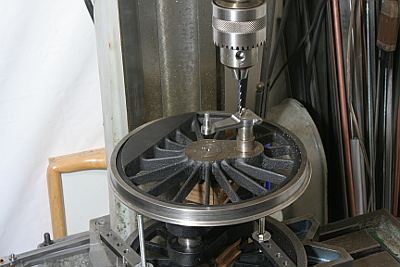
リターンクランクの角度を永久固定するため、軸と穴の境界にキーを打ち込む。実機は角穴になっているが、工作が困難なので丸穴で代用した。ドリルで穴を開け、穴よりわずかに太く仕上げたピンを打ち込んだ。
最後にエキセン棒を作る。これも他のロッドと同じ加工法だが、フルートが形成されている点が異なる。軸距は、さきほど治具で測定した数値のとおり、再びフライス盤のステージ座標を使って加工する。
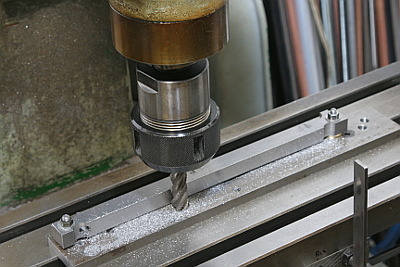
心向き棒と同様に、材料の大部分を削り落とさなければならない。ラフィングエンドミルで、上下面の肉削ぎ中。なお、軸距の異なる左右のエキセン棒を同じ治具で加工するため、材料の穴と固定ピンの間に、加工用の偏心ブッシュを入れている。
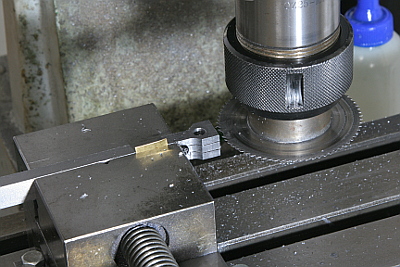
加減リンクと接続される全端部はフォーク形状となる。底をドリルで開け、底に向かってメタルソーで切り取り、エンドミルで仕上げる。
中央の薄い部分は、まず両端のアールを仕上げて、中央部を側面削りで削る。ここも延々と肉削ぎが続く。
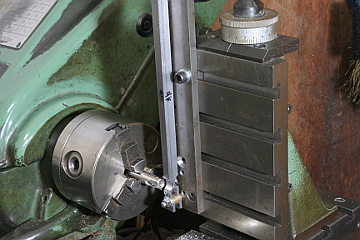
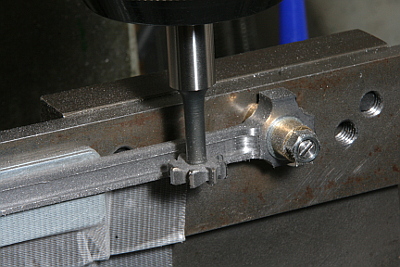
側面削りと同じセットアップで、フルートを加工する。深く切り込むとビビリが発生するので、0.15mm単位で削った。
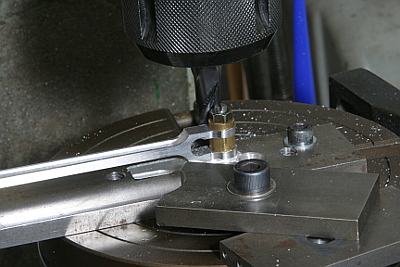
ロータリーテーブルでヘッドのアール加工をする。
フォーク根元の肩部分のアールもロータリーテーブルで加工する。加工するアールの中心は、フォーク底のクロス穴の中心と一致している。以下の手順でセットアップした。
- ロータリーテーブルの中心をフライス主軸に合わせる。
- フォークのクロス穴にセンターをケガいた真鍮丸棒を入れ、治具に取り付ける。
- ロータリーテーブル上に治具を乗せ、フライス主軸と丸棒のセンターを合わせた状態で治具をテーブルに固定する。
以後は、治具固定のまま加工物だけ入れ替えれば良い。
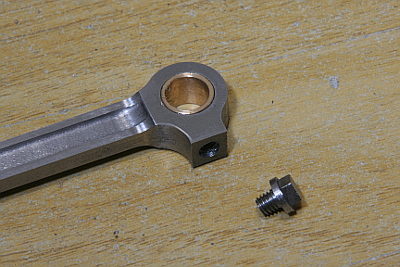
最後に砲金製のブッシュを圧入し、ダミーの油壺フタをねじ込んで完成となる。
ワルシャート式弁装置が完成した。2シリンダーだとこれでエアテストとなるが、3シリンダーなので、これからグレズリー式弁装置を作らなければならない。
目次 / 前月 / 次月