index / prev / next
< Gresley Valve Gear 2 >
The small lever is also made by steel flat bar. The center part connecting
to the large lever has a counterbore for a ball bearing. The both ends
are forked. I employed 12mm dia bearing.
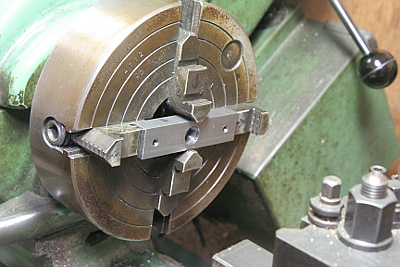
First, the counterbore is cut in the lathe. The photo shows cutting an
inner groove for a snap-ring after cutting the counterbore.
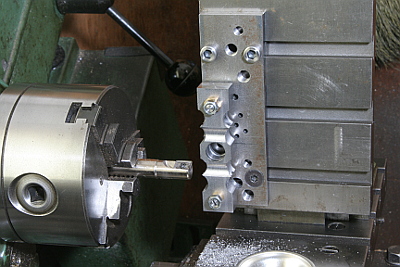
The inside radius cutting is done by end mill against the vertical slider on the lathe table.
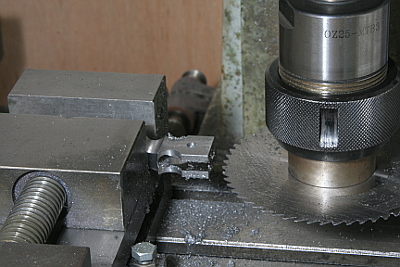
After drilling the bottom of a fork, open the fork by slitting saw.
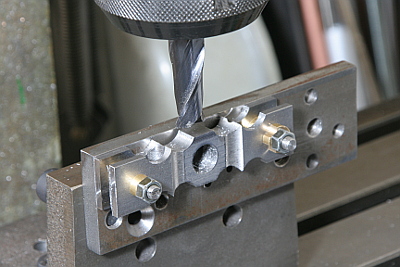
Finish side profile with the jig on an angle plate.
The both round heads and round center are finished in the rotary table.
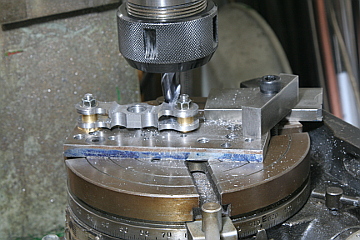
Shoulders of the fork are also finished in the rotary table. The left photo shows centering the zig with a brass rod into the round fork bottom.
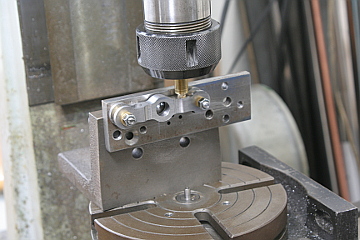
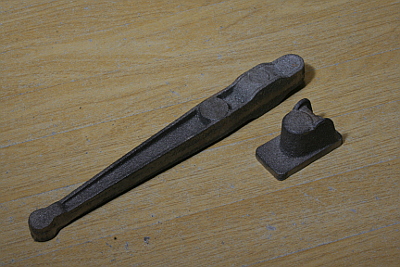
The large lever and the large lever bracket are cut from castings that
I prepared a long time ago (August 2009). There had been a chill at the
smaller tip of the large lever. As usual, it was removed by the electric
furnace. Heat up to 850 centigrade and cool down slowly in the furnace.
The large lever has 2 to 1 axle arrangement. It also has center bearing and both forked ends. The shorter forked end has large opened bottom that will hold the small lever center and clear the small lever end. The lever is too long to turn in the Myford lathe. So I had turned a bush with a precise counterbore from a round rod and glued the bush into drilled hole of the lever with Loctite.
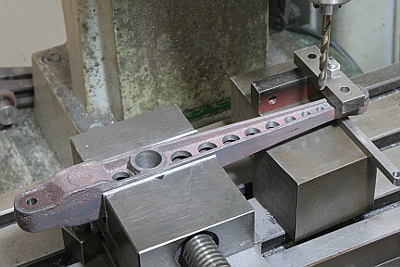
First, all of necessary holes are opened at a time. Note both the center part and one end are clamped. Position of each hole is controlled by x and y axis of the milling stage.
The large opened bottom is cut off with a series of drilling holes and finished by end mill. In the second photo, the vise is tilt in order to mill slanted face.
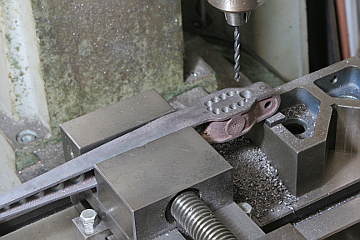
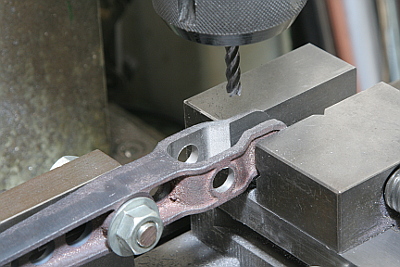
At last, the forked end is opened and finished by end mill.
The large lever bracket has a large c-shape cutout to hold the large lever.
Maximum diameter of the holes is 16mm. All of them are opened with drills.
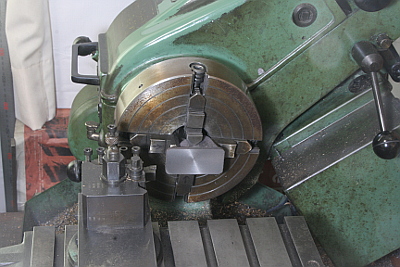
First, the bolting face is finished in the lathe.
The c-shape cutout is opened by band saw and drill, then finished by end mill.
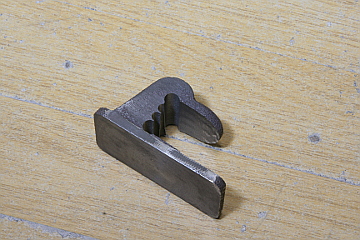
index / prev / next