index / prev / next
< Boiler Design >
The time has come to tackle with the boiler. My C53's boiler will be about
30 kilograms weight. Huge thermal power is required to silver solder such
a heavy boiler and is difficult to treat in a quiet residential area. So
I asked a club member to use his factory for the soldering operations.
The boiler is designed according to the model steam locomotive boiler standard
in Japan. I also refer the K-27 boiler of Kozo Hiraoka design. My boiler
is made from copper sheets and gunmetal bushes. Thickness of the sheets
are 2.5 mm for the barrel, 6 mm for the foundation ring and 3 mm for the
rest. The stays are made of 7 mm dia. phosphor bronze bar.
The blue drawings show side view of the boiler, while the gray drawings show scale-down of the full size boiler, that is too large for a model steam locomotive. Barrel's diameter, whole length and whole width are reduced. Front end of the barrel is 159 mm O.D. and the boiler whole length is 933 mm. According to the tilt backhead, firebox front and bottom are also tilt. So the section of the foundation ring is rectangle anywhere. The barrel is consist of two telescopic bodies and also the firebox outer wrapper rides on the barrel. As a result, the boiler profile is slightly taper as a whole, that is the same as the full size boiler. I designed the boiler details with 3D-CAD as follows.
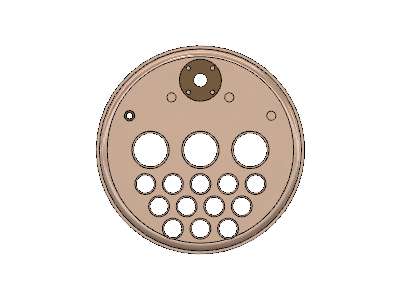
The boiler has twelve 16 mm O.D. tubes and three 28.5 mm O.D. flues. I
adopted larger size and smaller number tubes for C53 boiler because the
boiler's tubes are relatively longer than usual.
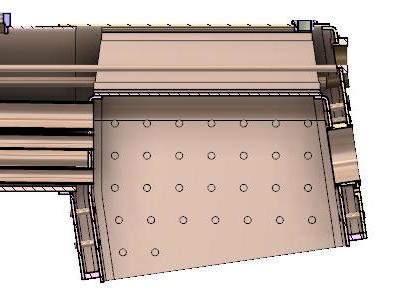
The firebox tubeplate and the throatplate are bent in the middle. Usually
they are bent after flanging with flat formers. But I will prepare bent
formers for them and do flanging and bending at a time. The backhead and
the inner backplate tilt forward. So their flanges are obtuse angle at
top and square at both sides. These also require special formers.
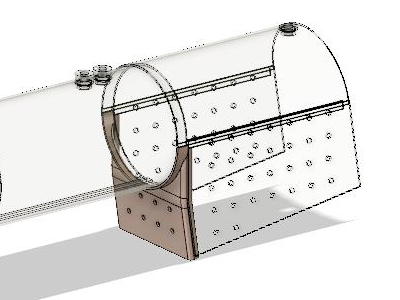
The throatplate must be the most difficult to fabricate for its complicated shape. It requires more than two formers and their designs are important.
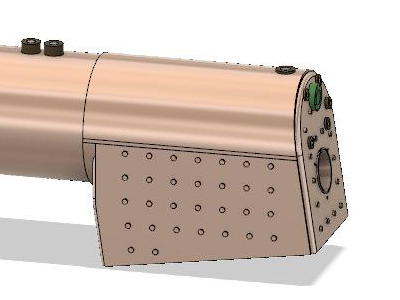
The regulator is parallel to the boiler barrel. So the regulator bush on the backhead is tilt against the backhead panel. It will be done by tilting the bush's profile, not by tilting the bush itself.
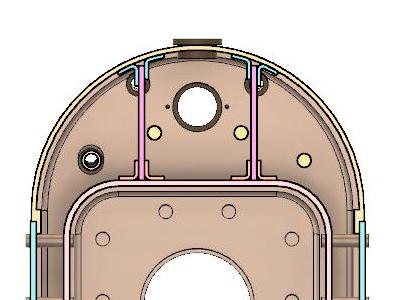
The crown stays are two vertical plates held by bent angle plates between
inner and outer wrappers.
Total weight of the boiler calculated by 3D-CAD is 28 kilograms. How much
thermal power is necessary in order to silver solder the boiler? Kozo's
K-27 boiler has already completed and its builder Mr. Nakahara utilized
Sievert #2944 burner (50 mm dia., 86 kilowatts) for its final soldering
operation. Weight of the boiler may be 14 kilograms. Therefore the burner
isn't enough for the C53 boiler. The maximum Sievert burner is #2960 (60
mm dia., 114 kilowatts). A Japanese supplier Shinfuji also provides a series
of propane gas torch and its maximum burner is PB-10H (100 mm dia., 167
kilowatts). I think it is the final choice. Incidentally, thermal power
of typical cooking stove is four kilowatts, so the burner is as strong
as 40 cooking stoves!
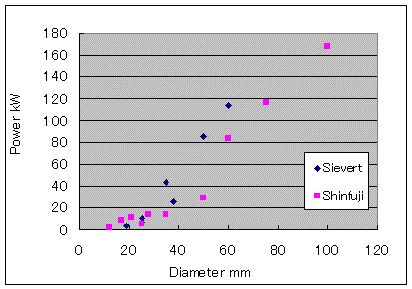
The chart shows comparison of Sievert and Shinfuji burner varieties with their diameter and power. Especially among larger size burners, Sievert is stronger than Shinfuji in the same diameter. But there is no limitation of burner diameter for our operation. So we can simply choose by required power.
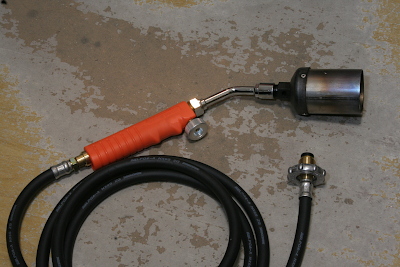
I got Shinfuji burner PB-7H (60 mm dia., 83.7 kilowatts) at the beginning.
For trial, I burned it at a moment in my home's small backyard. It sounded
as if a jet fighter passed overhead. I understood the tool is unbecoming
to quiet residential area.
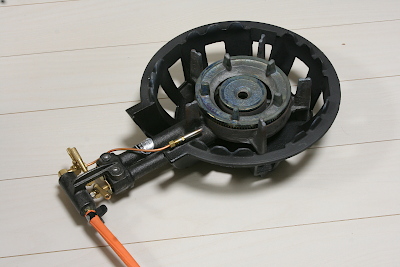
In order to anneal copper parts quietly at home, I also got a cast cooking
stove. It is for professional use and has two times stronger power than
usual cooking stove.
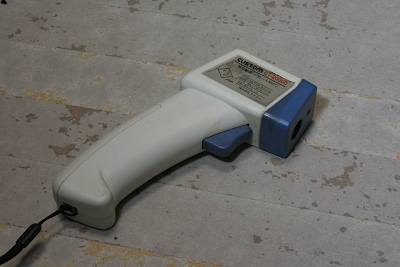
This is a radiation thermometer that I've been using for a long time. It
can measure only up to 550 centigrade, that is enough to control annealing.
The next is preparation of the formers.
index / prev / next