index / prev / next
< Boiler Formers >
Steel plate is ideal for the former of boiler flanged plate. But C53's
boiler is big and making steel formers is hard work. So I employed hard
wood for the formers. I chose American hard maple that is relatively cheap
and easy to get. It is enough hard to be threaded. I selected 20 mm thickness
plates. The opposite backing plates are also made from the same material.
Please refer the shapes of final copper plates shown last month. Here I
introduce finished formers and backing plates and then introduce their
making method.
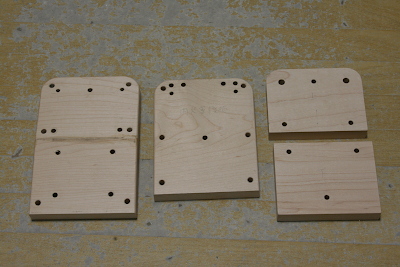
These are for the inner firebox. The leftmost one is a former for the firebox tubeplate and is bent in the middle. It is hard to cut out a bent plate from a wood blank, so I made it from two plates glued with epoxy adhesive. Practically it is enough withstand hard hammering work. The middle one is a former for the firebox backplate. It is a flat former but its cross section is tilt. The rightmost two plates are separated backing plates for the both formers.
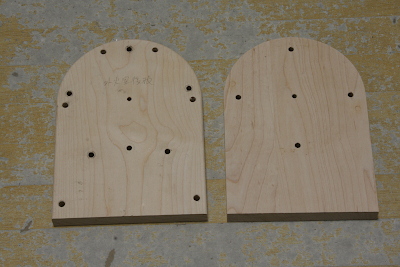
These are for the backhead. The left one is a former and the right one is a backing plate. They look the same but the former needs high accuracy and the backing plate can be cut roughly. Cross section of the former is also tilt.
For the throatplate, I need a number of formers and backing plates. The left side three plates in the photo are for the straight flanges at both sides. The upper one is a bent former that is made from two plates glued together. The lower two plates are divided backing plates. The right side two plates are for the half round flange. Both are formers for front and back faces.
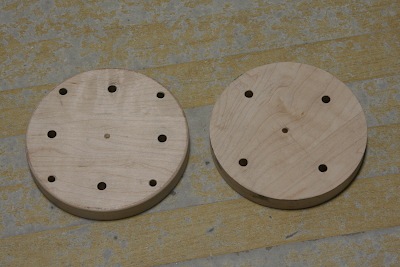
The smokebox tubeplate at the front of the boiler must be flanged, too.
It is simple disc shape and its former can be turned in the lathe. The
left one is a former and the right one is a backing plate.
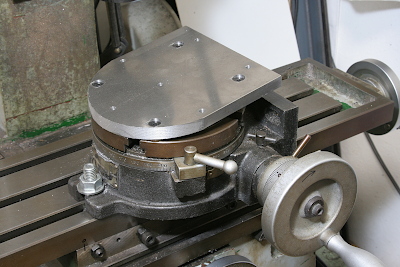
Cross sections of the firebox backplate former and the backhead former
are tilt, therefore they have to be set on the rotary table at specified
angle. First, I set a steel base at the angle on the rotary table. The
procedure is as follows.
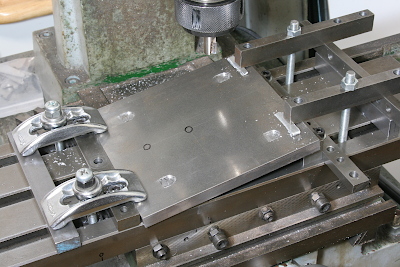
Tilt holes must be opened in the base. The base material is set on the
milling table in the angle and started from milling square face before
drilling and countersunk. Incidentally, other screw holes for fixing formers
are square to the base.
The photo shows columns in order to hold the base on the rotary table. Their inclined tops are cut by end mill.
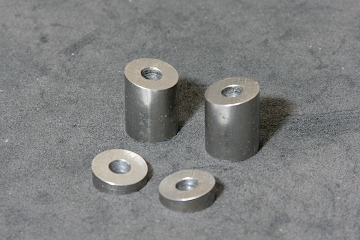
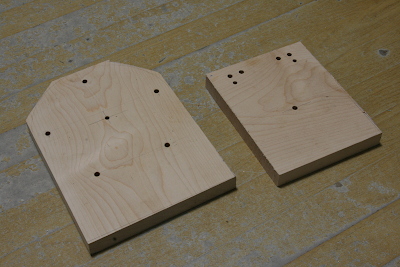
The formers materials are roughly cut out from a wood blank and drilled
fixing holes. The photo shows materials for inner back plate and backhead
formers.
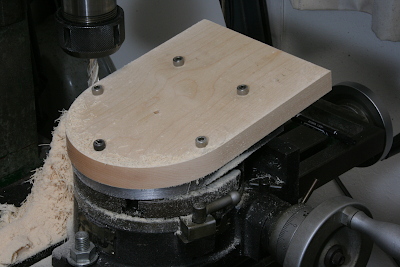
The materials are fix on the tilt base and cut section by end mill. The
photo shows cutting the backhead former.
Next, the firebox backplate former is cut. There are two radius centers in the former. Cut one radius and adjacent two sides, change position and then cut the other radius and the remaining side. There is a packing (invisible in the photo) between the former and the base, in order to dodge the end mill tip. During cutting both sides, the end mill height must be stepwisely changed.
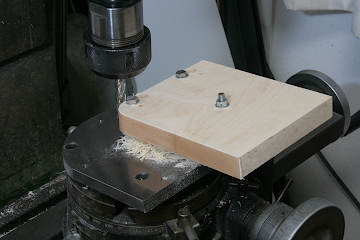
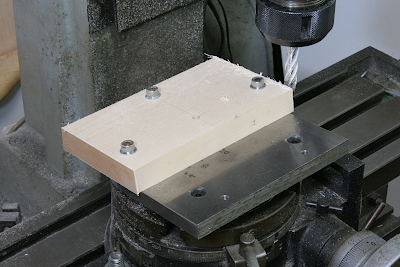
The photo shows cutting lower part of the throatplate former. There is no radius but the tilt base is useful to cut the former's tilt side. After that the tilt side is glued to a vertical side of the upper former and then I obtain bent shape of the glued former.
Top side edge of each former must be filleted. I employed a 3 mm radius cutter. The tilt base isn't useful here because the cutter height is constant.
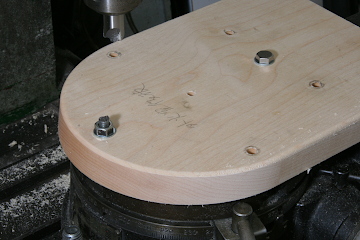
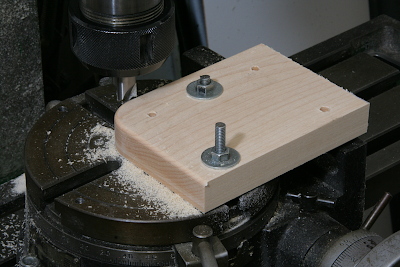
Upper part of the firebox tubeplate former has only vertical sides. So the blank is fixed directly onto the rotary table and then cut sides and fillet at a time.
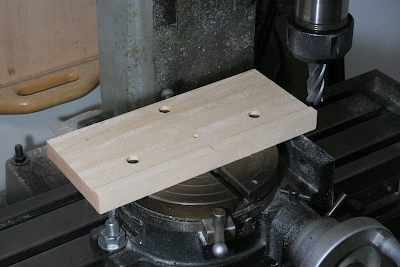
Lower part of the throatplate former has a step to hold the throatplate during hammering. The step is cut here by end mill.
The throatplate former's half radius is cut in the rotary table. The cut radius is almost the same as the rotary table outer radius, so I prepared a large steel base to expand the stage.
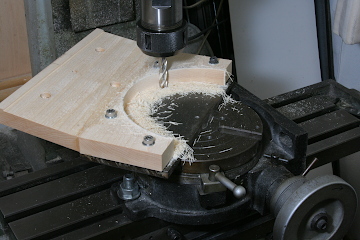
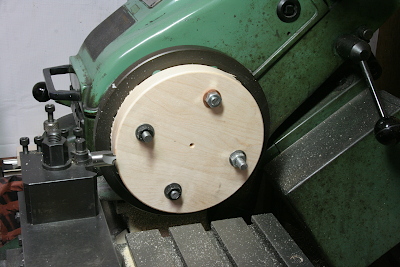
The former for the smokebox tubeplate is finished in the lathe. The photo
shows cutting fillet with a radius cutter held in the tool post.
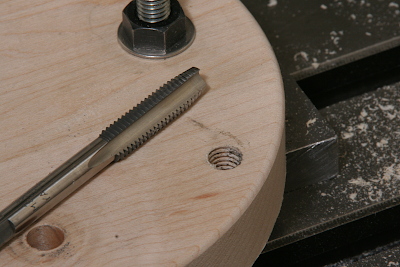
Wood former is sometimes compressed and becomes difficult to pull out from
copper plate. Just in case I opened screw holes so as to lift up the copper
plate. As noted above, the hard maple can be threaded with a tap for metals.
I used ISO M8 tap.
The backing plates are also made in the same manner as the formers but need less accuracy.
index / prev / next