index / prev / next
< Preparation for Silver Soldering >
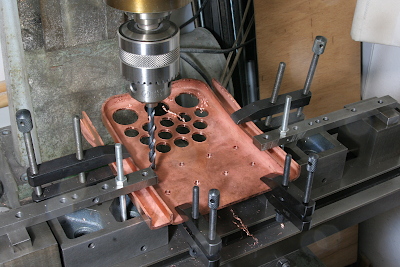
Front stay holes in the throatplate have not been opened yet. They are
drilled through the firebox tubeplate.
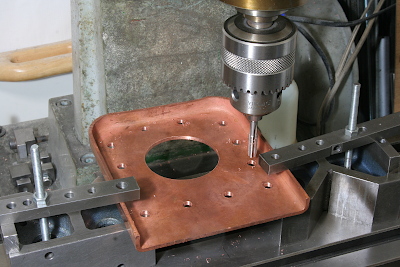
Tap the stay holes in the firebox tubeplate and the firebox backplate. Their size is M7 x 0.75.
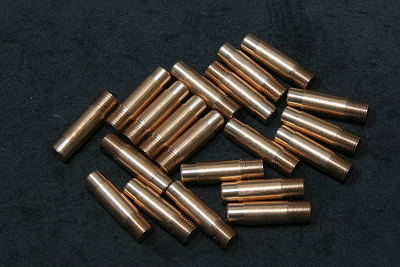
Make front and back stays from 7 mm dia. phosphor bronze rod. One end is threaded by M7 x 0.75 die, while the other end is turned down to 6.1 mm dia.
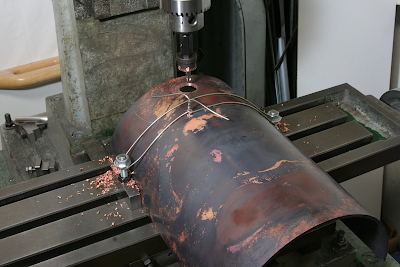
Hole for the steam turret bush in the outer roof is opened by a holesaw. Note the softened outer roof is fixed firmly by a wire.
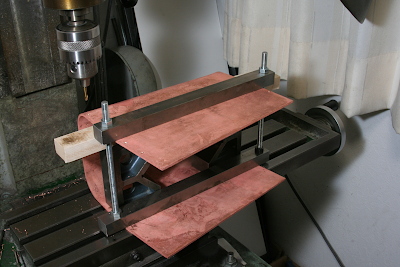
Drill holes for copper rivets on the inner wrapper. Drill 2 mm hole and cut 4 mm countersunk.
Drill the firebox tubeplate and the firebox backplate through the inner wrapper. Each hole is fixed temporary by M2 screw and nut.
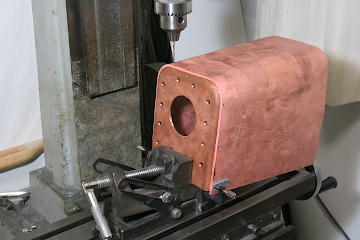
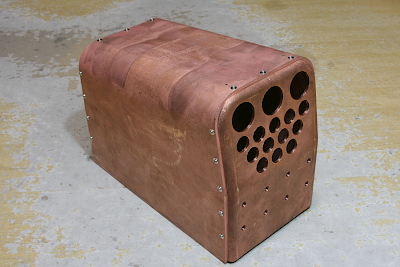
The firebox is temporary assembled. The screws and nuts will be replaced
with copper rivets before soldering.
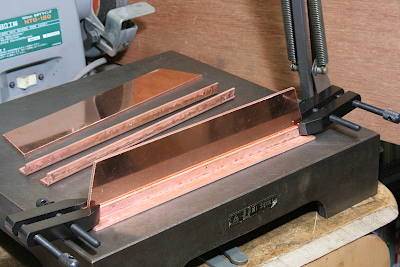
The crown stay is a vertical plate sandwiched by two angle plates. The angle plates are made from copper band plates fixed in the vise and bent by a plastic hammer. Open holes for rivets in an angle plate, combine and clamp one another on a surface table.
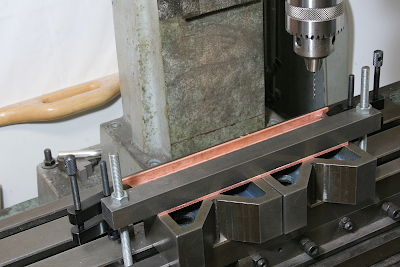
Put them down sideways and fixed on the table, and then drill through the holes for rivets. They are also fixed temporary by screws and nuts.
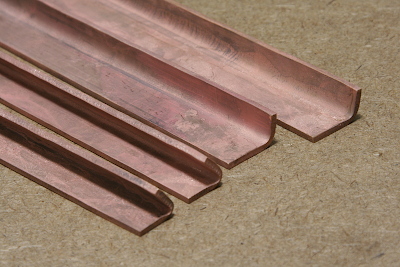
The upper angles for round tilt roof should be a pair of acute angle and obtuse angle.
The angle former is cut from a hard maple plate. A copper band plate is chuck in the bench vise with the angle former and bent by a plastic hammer.
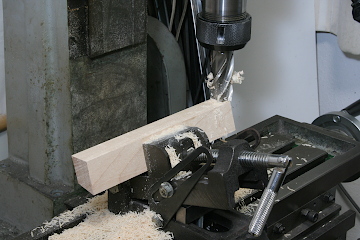
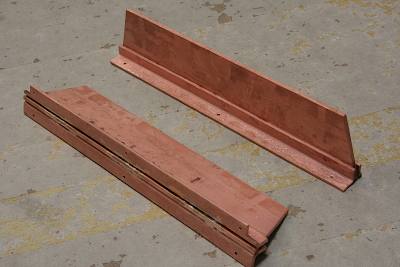
At first the crown stay vertical plates and lower angles are fixed by rivets
and silver soldered. So far, things can be done at home.
The crown stays are clamped on the inner wrapper and the holes for rivets are drilled through. There are also temporary fixed with screws and nuts.
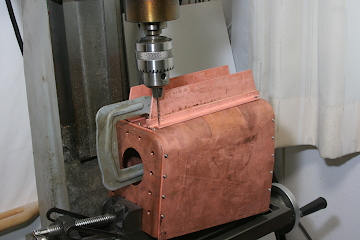
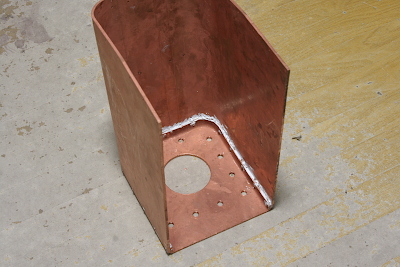
Followings are preparation for the first step silver soldering operations. First the firebox backplate will solder to the inner wrapper. Push rivet from inside and hammer tip into the countersunk. Line up 1 mm dia. silver solder short pieces and apply flux freely. Then dry up overnight.
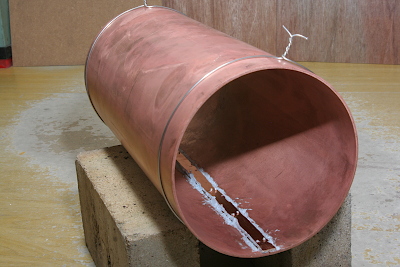
The barrel is patched up with a band plate that is tapped for screws. So the final assemble is not with rivets but brass screws from outside. 1 mm dia. silver solder pieces are lined up along both sides of the band plate, apply flux on the solder pieces and dry up.
Here I prepared a crimping tool. It is made from a silver steel bar. Cut like a bamboo spear, hardened and tempered. A bush is put into the backhead from bottom. Then around three points close to the bush are strongly push by the tool, then the bush is fixed firmly like a press fit.
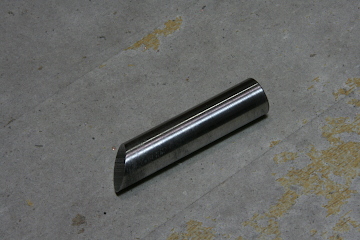
The next is the large silver soldering operations at a factory.
index / prev / next