index / prev / next
< Silver Soldering Operations #3 >
The third series of soldering operations were done. First, solder the wet
header bush on the smokebox tubeplate. The bush is put from below. Before
soldering, the bush was temporary fixed by crushing copper surface.
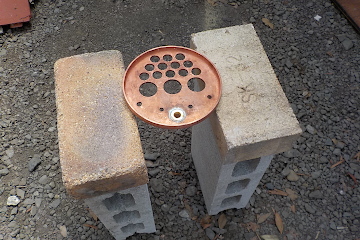
Solder the spare check valve bushes on the backhead.
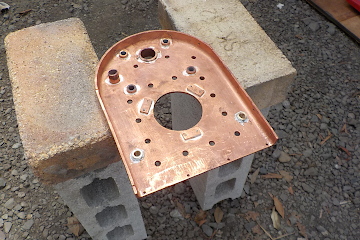
This time I tried an oxy-propane torch that is recommended by a club member.
The tool is between the oxy-acetylene torch and the propane gas torch.
The power is relatively strong, as its 30 mm dia. nozzle is stronger than
my 70 mm dia. nozzle propane gas torch. It means the fire temperature is
comparatively higher than the propane gas torch. Special care must be taken
not to melt copper material.
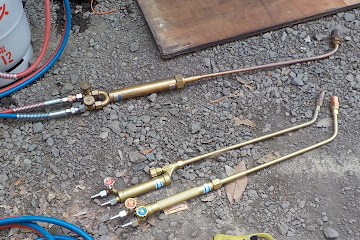
Solder the prepared throat plate and firebox roof plate riveted on the barrel. Here I tried the oxy-propane torch. As long as I keep the nozzle in reasonable distance from the job, it works like a propane gas torch. Required time to melt the solder is almost the same.
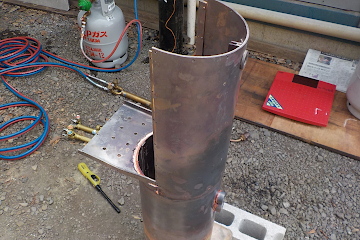
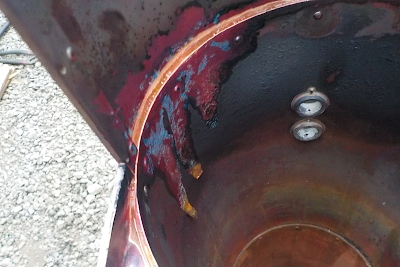
After soldering, I checked the seams and found lack of solder in some part
around the barrel. So I added solder and flux, and heat up the job again.
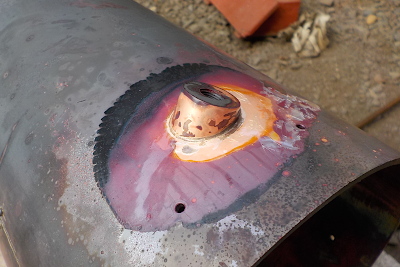
Solder the check valve bush on the front barrel, which I had forgotten in the first soldering operation. Fix the bush by two brass screws from inside, and flush solder from outside.
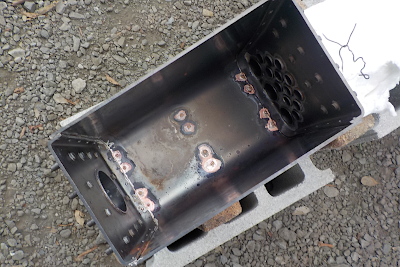
Here I add a solder on the rivet heads in the firebox. The rivets are for the crown stay.
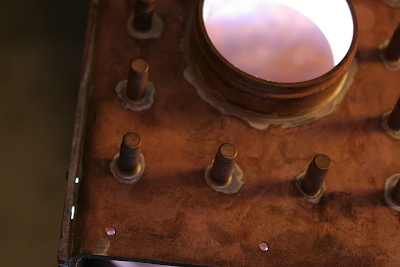
At home, I inspected the whole job with a flashlight in a dark room and found a nasty chink between the inner wrapper and the back plate that I was worried because the gap is too much at the first soldering operations. Maybe once filled solder flowed out at repeat soldering operations.
If I just fill solder again, maybe the chink will appear again after the final soldering operation. So I tried to plug the gap itself with a shim, as follows.
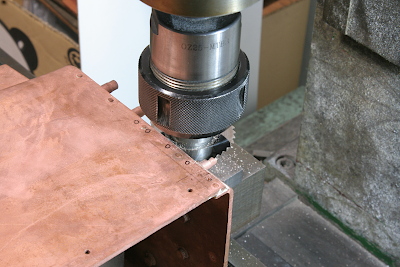
Start separating the defect area by a metal saw. The gap is 0.2 mm, so I use 0.3 mm thickness metal saw to cover the gap.
Cut continuously with a fretsaw, in order to eliminate round profile by the metal saw radius. When sawing, the side face of the fret saw blade should be touch with the wrapper's inside face. But the fret saw handle stands in the way. Therefore I add a part in the handle to bend the fret saw blade side-over the handle.
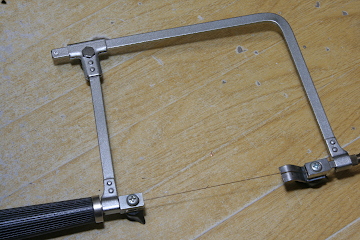
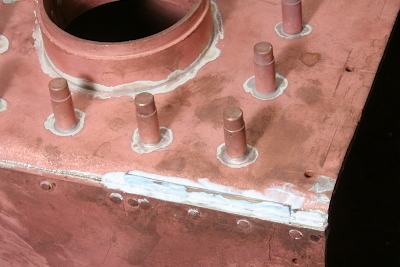
Plug the gap with 0.3 mm thickness phosphor bronze sheet and close them
firmly with additional copper rivets. Finally, apply the flux and prepare
for the next soldering operation.
index / prev / next