index / prev / next
< Silver Soldering Operations #5 >
This is the last to do soldering operations except for repairs. The operations
continued for three days.
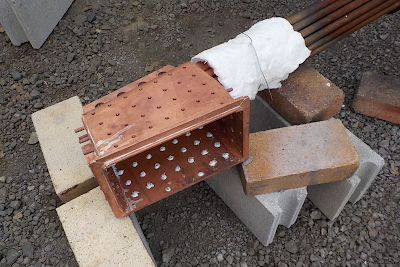
The side stays are first soldered only in the inner firebox. Screw the side stays from the outside, set silver solder rings in the firebox, apply flux, heat from the outside until the melt solder flows out. It needs two times operations for the both sides.
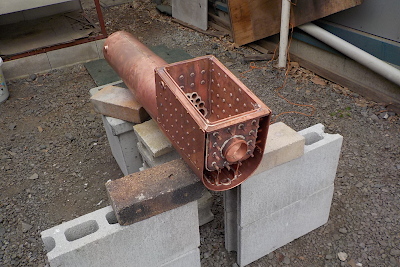
The inner and outer boilers are put together and connected by the two side plates. These are the whole boiler components without the backhead and the smokebox tubeplate. Not shown in the picture, the front ends of the large tubes are held by a horizontal plate inserted in the barrel, so as to prevent hanging down of the tubes.
The crown stays and the angle plates in the outer firebox are soldered. Put 1 mm dia. silver solder wire along both sides of each crown stay, and heat from back. I employed propane-oxygen torch with relatively small nozzle, so as to put the nozzle deep into the outer boiler without lack of oxygen.
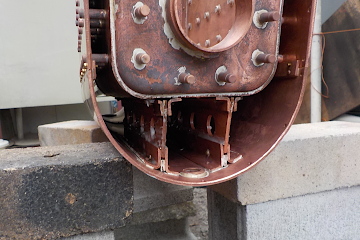
The side plates are once removed and pickled respectively. Assemble again with the backhead and put silver solder rings around the side stays. Also put a silver solder wire between the roof plate and the side plate. Apply flux and heat from the outside. At this stage, the heat capacity is goodly amount and I adopt brand-new 75 mm dia. nozzle.
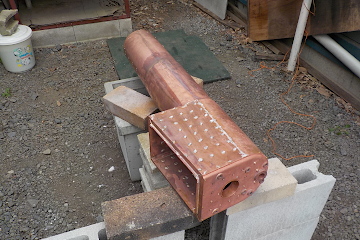
Even with the larger 75 mm dia. nozzle, it took ten minutes to complete the soldering operation. It let me down and I restored to the old 60 mm nozzle and repeat the operation for the opposite side. It resulted almost the same operating time. I guess, with the larger nozzle, the flame diffuses and the heat loss increases. Only the gas consumption is larger than the smaller nozzle. After all I employed the old nozzle and continued the rest of operations.
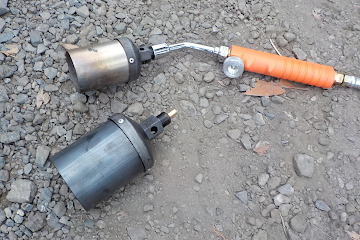
Front stays and both sides of the throat plate are soldered. As the heat area is relatively small, the soldering operation was finished in five minutes.
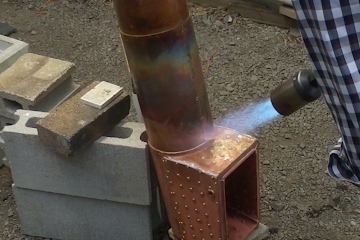
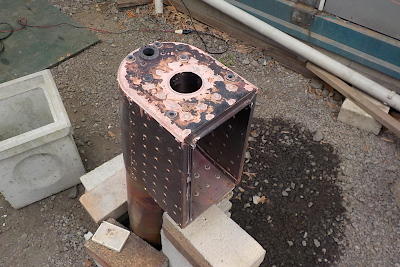
The backhead surroundings, the firehole and the backstays are soldered. It took maximum fifteen minutes to complete the operation. It exceeded the effective time of the flux, so I added flux on the way.
Flow solder between the outer firebox and the foundation ring. Start at a point, confirm melting of the solder, go round the foundation ring slowly and flow all of the solder. It took ten minutes.
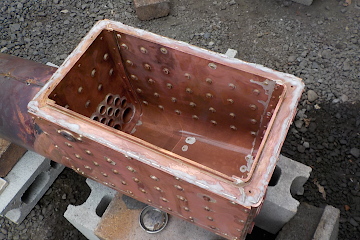
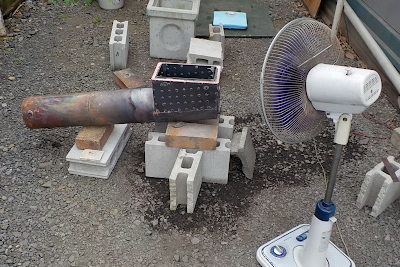
With the larger amount of heat capacity, the cooling time becomes longer and longer. It took more than one hour to the room temperature. So I adopt a cooling fan. It was very effective and shortened the cooling time one-third of natural cooling time.
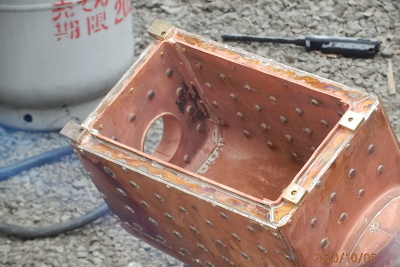
The four boiler shoes are screwed under the foundation ring and soldered. The shoes themselves are small but the foundation ring has large heat capacity, so it took long time.
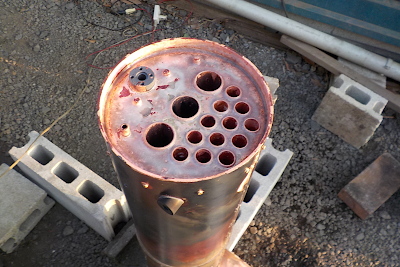
At last the smokebox tubeplate is soldered. The tubeplate surroundings, longitudinal stays, hollow stays, the tubes and flues are soldered. In order to protect the tubes and flues, ceramic sheet are packed in the tubes and flues at five centimeters depth from the top.
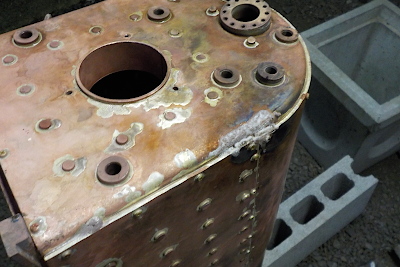
After all, the whole boiler is pickled and carefully visual-inspected. I found a lack of silver solder fillet at a corner of the backhead. So I added silver solder on the corner.
All of the silver soldering operation were finished. This time I didn't have enough time for the pressure test. I will report next time.
index / prev / next