目次 / 前月 / 次月
2023年8月 「炭水車本体(1)」
炭水車は、外壁をそのまま水槽として使用するのが一般的である。そのためボディ材質は、真鍮またはステンレスが好ましい。型式は、C53用で一般的な「12-17炭水車」としたが、戦前の炭水車のため、水槽表面に無数のリベットが露出している。リベットは加工の簡単な銅丸リベットを使用する。ボディ材は無数の穴を開ける必要があり、ステンレス(SUS304)では加工が大変なので、真鍮板を使用することにした。
人の乗車を考えると、強度的に板厚3mmは欲しいところだが、重たくなるし加工も大変なので、2mmを基本として、乗車位置をステンレスのアングルで内側からサポートすることにした。組み立てには真鍮のアングルを用いて、銅リベットと真鍮ネジで組み上げ、シールが必要な部分にはハンダを流す。側板と後板の継ぎ目はアール加工が必要で、板厚2mmだと加工が難しいため、後板だけ1.2mmとして、両端にアール加工を施し、アールの直前で側板と接合する。後板はアングル材で補強する。ボティ上端の縁取り材も1.2mmの真鍮を用いる。ハンドポンプを始めとする配管類は、基本的に水槽内に水没させる。走行による水の搖動を抑制するため、半仕切板で水槽を4分割する。中央の仕切りは、完全に塞げる構造にして、必要に応じて水槽の水量を半分に減らせるようにする。水槽の側部に、水を入れ過ぎた場合に自動排水する溢れ管を設ける。以上の前提で、設計を行った。
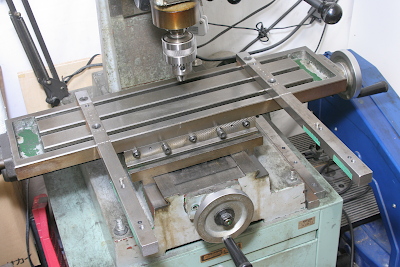
本体材料はフライス盤で穴開け加工などするが、ステージよりはるかに幅の広い材料を固定するために、平鋼2本をステージと垂直に固定して、ステージを延長した。
延長用の平鋼は、2本まとめて必要な加工をした。先端は、エンドミルで端部を加工する際に刃先を逃がすため段差を設けた。さらに、平行出しピンを刺すためのリーマ穴を随所に設けた。治具をステージに固定する際は、ダイヤルゲージを使い、正確に垂直平行を出した。
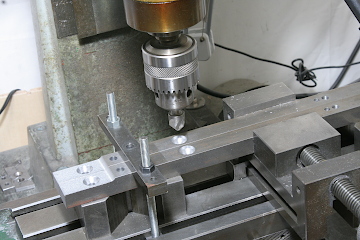
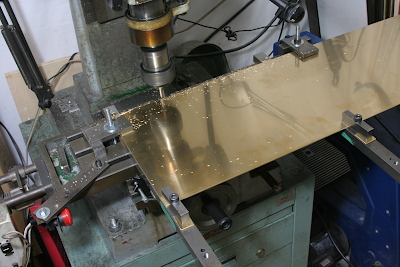
2mmの真鍮板から側板を切り出し、上下辺をエンドミルで仕上げる。片側を仕上げて、仕上げた側をピンに当てて平行を出し、対辺を平行に仕上げる。
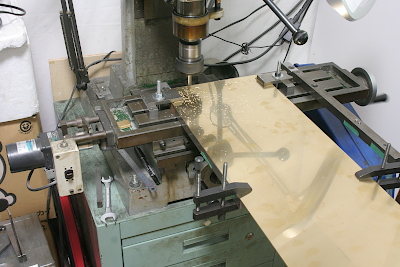
側板の前後辺を仕上げ。縦にセットする際は、仕上げた辺を平鋼のエッジに合わせて、ステージとの直角を出した。
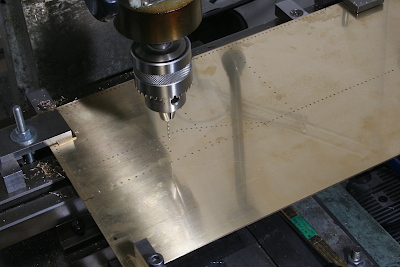
同様のセットアップで、側板にリベットの穴を開ける。1.6mmの銅リベットを使用するが、1.6mmドリルだと圧入気味になるので、1.7mmドリルを使用した。穴の位置は、フライス盤ステージの座標管理で求める。作業を楽にするため、穴のピッチはダイヤル一回転の2.5mmの倍数に設定した。センタードリルで連続してスタート穴を掘り、ドリルに持ち替えて連続で穴を貫通させる。側板全長がステージの移動量より長いので、セットアップを三度に分けて穴を開けた。
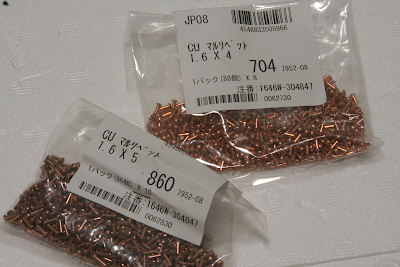
リベットは、ダミーとして単独で使用する箇所と、真鍮アングル固定に利用する箇所に分けて、長さを二種類用意した。必要数は、合計で1500本以上になる。穴開けもその回数が必要で、かなりの時間を費やした。
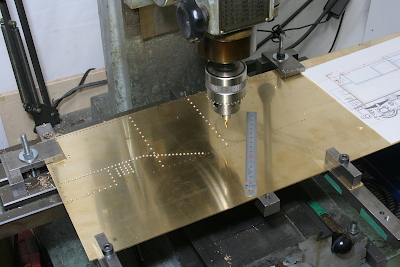
側板のリベット穴のうち、リベットを単独で固定する箇所については、穴の裏側を皿モミカッターで皿穴化し、リベットを潰して埋め込めるようにした。アングルを固定する部分については、アングルの穴を皿穴化することになる。
1.2mm真鍮板から後板の材料を切り出し、両端にアール曲げを施す。まず、アングルと丸棒で90度まで曲げたが、これだけだと、スプリングバックにより鈍角までしか曲げられない。
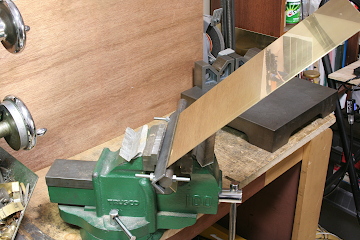
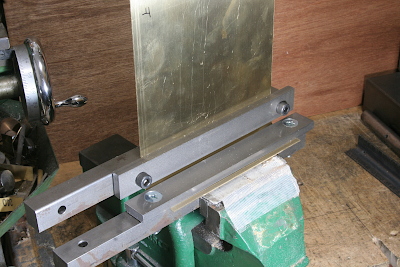
追加の曲げは、アールの両側のストレート部を平鋼で挟み、アール部分はフリーの状態で曲げた。片側の曲げの結果から、反対側の治具の位置を決めて、設計通りの幅が得られるようにした。
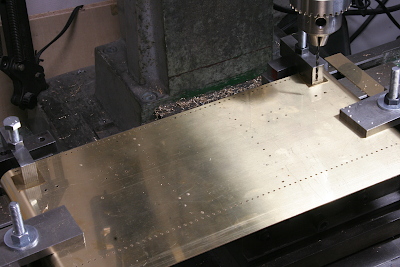
後板への穴開けは、両端を曲げてから行う。曲げの結果から正確に中心線を出すためである。
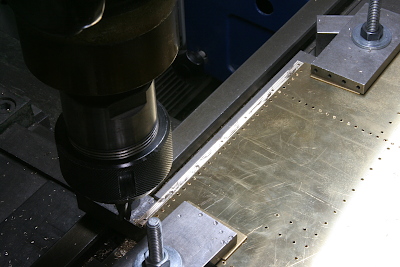
側板と後板の接合部は、側板を段差加工し、重ね合わせでツライチに合わさるようにする。段差加工はエンドミルで行った。板厚2mmのものを1.2mm削り取った。
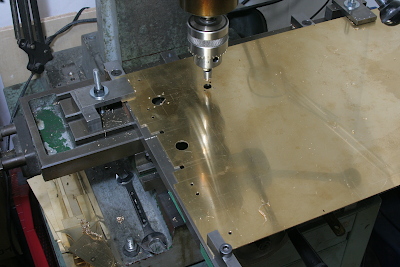
底板も2mmの真鍮板を用いる。器具類などを固定するための穴を開ける。写真はホールソーで穴を開けているところ。
目次 / 前月 / 次月